Aunque la calidad, consistencia y la entrega a tiempo son factores importantes en la mercadotecnia de hilados, no hay ninguna duda que los costos desempeñan un papel dominante en el marketing. Las Figuras 1 y 2, que están basadas en datos históricos de la Federación Internacional de Manufactureros Textiles (ITMF), de Zurich, Suiza – recopilados de varias ediciones de la “Comparación Internacional de Costos de Producción” de la ITMF – para la manufactura en Estados Unidos, representan el costo de la producción de hilos para hilos de algodón peinado elaborados en anillos e hilos de algodón cardado elaborados en rotores.
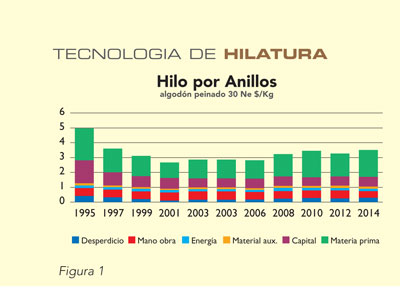
Figura 1
De acuerdo a estas cifras, es evidente cuáles son los factores que ejercen un impacto más significante en el costo total de elaboración del hilo. La Tabla 1 muestra que el costo del material en rama domina el costo final del algodón, y representa el 52% del costo total para la hilatura por anillos, y el 72% del costo total para la hilatura a rotores. Aunque hay diferencias en porcentajes de componente para los sistemas de hilatura seleccionados, es aparente que para minimizar los costos del hilo, los costos que se deben controlar son las materias primas, los desperdicios, la energía, y la mano de obra.
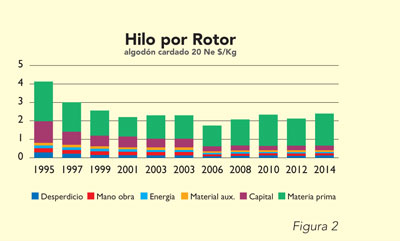
Figura 2
Materia prima
Las materias primas y los desperdicios, aunque son usados independientemente por la ITMF, son considerados conjuntamente puesto que cabe duda que la selección de la fibra puede desempeñar un gran papel en la cantidad de desperdicios producido durante los procesos de hilatura. Ciertamente, se ha dicho que es posible mejorar una materia prima de inferior calidad, por medio de la limpieza e incluso procesos de peinado, pero esta práctica obviamente aumenta los desperdicios.
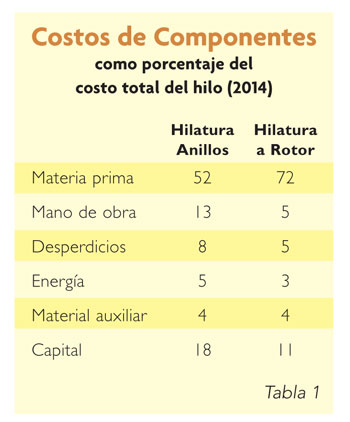
Tabla 1
Tradicionalmente, el contenido de fibras en el desperdicio era bastante constante, y por consiguiente, si la cantidad de remoción de desperdicios era doblada, entonces la cantidad de fibras perdidas también se doblaba. El pensamiento actual es que, debido a que la materia prima constituye un costo mayor, se deben hacer esfuerzos para optimizar los procesos, de modo que se efectúe una limpieza efectiva con una mínima pérdida de fibras.
Esto puede ser evidente por las tendencias observadas en las máquinas de apertura y cardado, en donde un diseño mejorado, que permite un mejor control del flujo de aire, se puede acoplar con sistemas de monitorizado sofisticado para evaluar el contenido de fibra en el tabaco. El control es obtenido por medio del cambio de los ajustes de la unidad de extracción de desperdicios (Ver Figura 3).
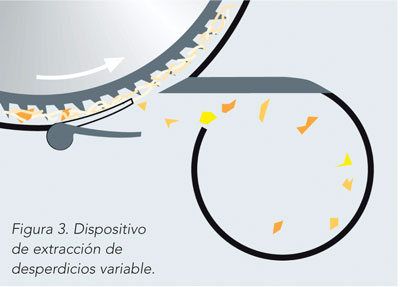
Figura 3
La Figura 4 ilustra cómo es posible incrementar la remoción de desperdicios sin el incremento usual de pérdida de fibras. Una solución complementaria es la recuperación de fibras por medio del reprocesamiento de los desperdicios generados en el salón de soplado, así como en el cardado y peinado.
Un aspecto adicional cuando se considera los desperdicios es el impacto potencial ejercido por las fibras foráneas y otros contaminantes. Estas impurezas de las pacas, si no se remueven al principio del proceso, pueden conducir a mayores problemas de contaminación, ya que las fibras son redistribuidas durante el doblado y el mezclado.
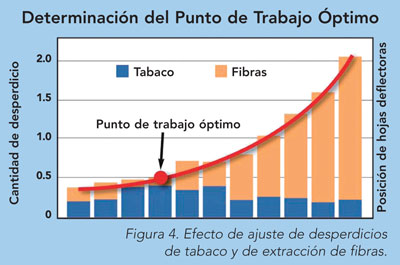
Figura 4
Se han hecho grandes desarrollos en el uso de diferentes fuentes de luz y sensores, de modo que las fibras foráneas que son del mismo color pero químicamente diferentes de la materia prima original, se puedan identificar y remover (Ver la Figura 5).
La detección de fibras foráneas se puede efectuar también durante procesos posteriores, incluyendo el purgado del hilo; sin embargo, la solución más lógica parece ser la eliminación temprana del problema.
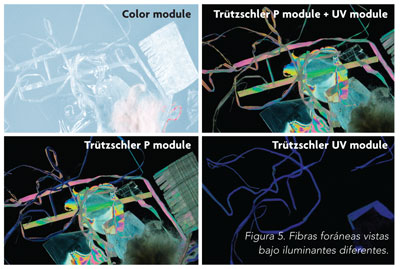
Figura 5
Se podría argumentar que el mayor uso de mandos múltiples en las máquinas de hilatura podrían permitir una óptima utilización de la fibra, debido al potencial de hilar varios lotes más pequeños en una sola máquina de hilatura, tal como la Autocoro 8, manufacturada por Schlafhorst Zweigniederlassung der Saurer Germany GmbH & Co. KG, de Alemania, lo que podría resultar en menos desperdicios.
El uso de automatización a través del proceso de hilatura ha reducido los defectos, y esto, a la vez, ha ejercido un impacto beneficioso en el desperdicio potencial. Parece inevitable que habrá un crecimiento continuo en la utilización de la hilatura a chorro/vortex, y habrá más esfuerzos para reducir la pérdida significante de fibras que ha sido asociada con esta tecnología.
Mano de obra
Los modernos salones de hilatura son tecnológicamente avanzados y el creciente uso de la automatización ha permitido que se pueda minimizar el componente relacionado con la mano de obra en los costos de producción del hilo. La conversión de pacas de fibras a cintas es esencialmente una etapa de procesamiento, y el uso de sistemas de monitorizado y control aseguran que muy poca intervención humana sea necesaria durante esta etapa de procesamiento.
Un componente adicional, particularmente en el procesamiento del algodón, es el uso de datos HVI de la paca en conjunción con el software apropiado, tal como el sistema EFS, ofrecido por Cotton Incorporated, de Cary, N.C., para asegurar la óptima utilización de las fibras.
Este método también asegura un mezclado de fibras de alta calidad, lo que a su vez permite una alta eficiencia durante la hilatura. Ciertamente, la interacción entre las propiedades de la fibra y los ajustes de la maquinaria es extremadamente crítica en la determinación de la última calidad, tanto del producto como del proceso.
Funciones de automatización, tales como la auto-igualación, los sistemas de transporte de mudada automática, la limpieza automática, y la colección automática de datos para procesos y productos, son de uso común; y la hilatura a rotores y a chorro/vortex, junto con el bobinado, utilizan también el empalmado automático.
Estas características reducen el componente de la mano de obra en el procesamiento, y por lo tanto, los costos de manufactura total. Aunque la automatización ofrece el potencial de obtener ahorros significantes en mano de obra, esto es generalmente acompañado por una reducción en la flexibilidad, puesto que el balance de producción entre maquinaria diferente se puede disturbar por cambios en los requerimientos del título o de torsión del hilo.
Puesto que un incremento en la productividad de maquinaria significa ge-neralmente que se necesitan menos máquinas para producir la misma cantidad de hilo, esto ejerce también un impacto en las necesidades de mano de obra. Diferentes manufactureros han usado métodos diferentes para alcanzar una mayor productividad, lo que se refleja en el material publicitario, y así, para el cardado, se hicieron las siguientes declaraciones en la ITMA 2011 efectuada en Barcelona, España:
- La Carda de Alto Rendimiento C70, del Grupo Rieter, de Suiza, se describió como “la carda con la máxima área activa de cardado”.
- Trützschler GmbH & Co. KG, de Alemania, afirmó que su carda TC11 tiene “la mayor sección de cardado en el mundo”.
- La carda Galileo C701, de Marzoli S.p.A., de Italia, se describió como la carda “con la mayor superficie de cardado en el mundo en la actualidad”.
Los diferentes manufactureros obtienen los incrementos en productividad a través de una combinación de un ancho mayor de la máquina acoplado con una mejor geometría, de modo que se pueda obtener una máxima utilización de toda la superficie de cardado disponible.
De manera similar, la maquinaria de hilatura por anillos ha experimentado un incremento en el número de posiciones de hilatura por máquina – hasta 1.840 – lo que es beneficioso para reducir el costo de la automatización por máquina mientras que reduce al mismo tiempo el número de máquinas necesarias para alcanzar los mismos niveles de producción.
Además, lo que parecen pequeñas mejoras tecnológicas ejercen también un impacto en los requerimientos de la mano de obra, tanto en la manufactura de hilos como en los procesamientos subsiguientes. Un ejemplo de tal cambio es la habilidad de construir paquetes de hilo que contienen más hilo; y compañías tales como Schlafhorst claman que pueden acomodar hasta un 20% más de hilo en sus propios paquetes de hilo open-end.
Esto no solo significa que hay una menor necesidad de frecuencia de mudadas, lo que mejora la eficiencia de operación, sino que se requiere menos mano de obra en los procesos posteriores, puesto que los paquetes suministrados necesitarán ser cambiados de manera menos frecuente.
Dr. William “Bill” Oxenham es Profesor Abel C. Lineberger, así como Decano Asociado de Programas Académicos del Colegio de Textiles, de la Universidad Estatal de Carolina del Norte, en Raleigh, N.C.
Julio-Agosto de 2015