E
l cáñamo tiene una larga historia de uso en textiles. Debido a su inherente resistencia
la abrasión y a la desintegración, así como su alta resistencia a la rotura, esta fibra basta larga
fue usada en productos tales como veleros y cuerdas.
Su cultivo no requiere el uso de pesticidas, y no requiere irrigación, excepto en casos de
sequía. Esta fibra crece en una amplia área geográfica y climática. En años recientes, a medida que
ha crecido el interés en las fibras cultivadas orgánicamente y en los procesos de producción amenos
al medio ambiente, el cáñamo ha encontrado un mercado tipo nicho para uso en prendas de confección
orgánicas.
Uno de los primeros líderes en este mercado, la firma Hemptown Clothing Inc. – conocida
ahora como Naturally Advanced Technologies Inc. (NAT), con plantas de producción en Portland, Ore.,
y en Vancouver, B.C., Canadá – ha tornado su atención a la producción de fibras de cáñamo usando
procesos innovativos y que se son amenos al medio ambiente.
La firma Crailar® Fiber Technologies, subsidiaria de NAT en Vancouver, en asociación con el
Concilio de Investigación Nacional de Canadá y el Concilio de Investigación de Alberta, ha
desarrollado dos tecnologías para el procesamiento de cáñamo: Crailar Organic Fibers, y Crailar
Advanced Materials.
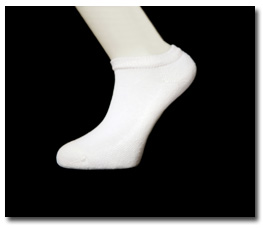
Fibras Orgánicas Crailar®, blancas y suaves,
se pueden procesar en sistemas de hilatura de
algodón tradicionales, y se pueden mezclar también con
algodón para numerosas aplicaciones en confecciones.
Crailar Organic Fibers
En el proceso Crailar Organic Fibers (Fibras Orgánicas Crailar), las fibras de cáñamo son
cortadas en longitudes de 1.5 a 2 pulgadas y son procesadas en en un baño enzimático de circuito
cerrado usando un equipo especializado para la producción de una fibra blanca y suave que es
parecida al algodón.
“El sistema de procesamiento remueve todos los desperdicios, dejando una fibra que es fina,
suave y completamente separada y que se puede cardar e hilar en sistemas de hilatura de algodón
tradicionales”, explicó Ken Barker, CEO de NAT.
Hace dos años, el fabricante de prendas Hanesbrands Inc., de Winston-Salem, N.C., patrocinó
ensayos realizados en el Colegio de Textiles de la Universidad Estatal de Carolina del Norte,
efectuados con el fin de evaluar la viabilidad comercial de los tejidos elaborados con una mezcla
de hilados de algodón y Crailar Organic Fiber.
Los ensayos mostraron que la adición de Crailar podría proveer ahorros significantes en los
costos, debido a una reducción en el encogimiento y a una reducción en el requerimiento de
colorante. Los tejidos exhibieron también una mayor resistencia a la rotura y mejores capacidades
de absorción de tipo mecha.
NAT ha firmado un acuerdo de desarrollo conjunto con Hanesbrands que incluye el
retro-equipado de equipos colorantes en una planta de Hanesbrands para procesar productos de
Crailar/algodón para uso en las confecciones.
En otro acuerdo, el teñidor a comisión G.J. Littlewood & Son Inc., de Filadelfia,
procesará fibras para los socios de NAT en las confecciones y proveerá a los hilanderos con ensayos
de muestras.
Un acuerdo de licenciamiento de marca registrada con el hilandero industrial Patrick Yarns,
de Kings Mountain, N.C., involucra la producción de hilados para uso en muebles para el hogar y en
alfombras, así como también en tejidos de denim, ropa para trabajo, y otros tipos de confecciones.
Crailar Advanced Materials
La tecnología de Crailar Advanced Materials consiste de un proceso de pulpado que no usa
substancias químicas fuertes y que es más económico que los equipos de pulpado tradicionales usados
en la industria. Baker dijo que este proceso mantiene la integridad de la estructura celulósica del
cáñamo y que permite aumentar el rendimiento.
Esta tecnología utiliza también un proceso de lyocell para elaborar un hilado extrusado que
puede ser modificado para ofrecer propiedades hidrofóbicas, al mismo tiempo que ofrece propiedades
hidrofílicas inherentes.
“Este será el primer hilado de rendimiento que es verdaderamente sostenible”, dijo Baker.
Además, la pulpa se puede usar en bioplásticos y se está sometiendo a ensayos para tratar sus
propiedades relacionadas con la elaboración de papel.
Fibra kenaf
La membrana de arquitectura Kenafine®, manufacturada por Taiyo Kogyo, y vendida en América
del Norte por la firma Birdair, se puede reciclar en productos de papel al final de su vida útil.
Kenaf es una planta que crece con rapidez y que absorbe el bióxido de carbono a una de las
tasas más elevadas de cualquier planta. Esta planta está ocupando su lugar en la arena de la
arquitectura sostenible como una materia prima que se usa en una membrana de tejido arquitectónico,
de bio-masa amena al medio ambiente, y que se puede usar en instalaciones temporales para la
cobertura de grandes áreas, pero que al final de su vida útil se puede reciclar completamente en
productos de papel que tradicionalmente se fabricarían de pulpa de madera.
Birdair Inc., de Buffalo, N.Y., es un diseñador y fabricante de estructuras livianas de alta
resistencia, así como de sistemas de techo de gran expansión. La firma es miembro del grupo japonés
Taiyo Kogyo, y está ofreciendo en Norte América la membrana Kenafine®, fabricada por Taiyo Kogyo.
De acuerdo a la compañía, la Kenafine® es la primera y única membrana de tejido arquitectónico que
es completamente reciclable, y está disponible en todo el mundo.
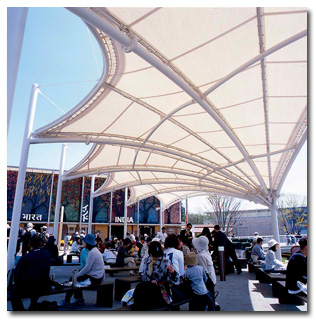
Esta estructura de cobertura de
protección contra el sol fue exhibida como una membrana
de tejido arquitectónico de la marca Kenafine®
durante la Expo 2005 realizada en Aichi, Japón.
La versión más reciente de esta membrana está siendo
ofrecida en Norte América por la firma Birdair Inc.
La fibra basta de la planta kenaf, un miembro de una familia de tallos que incluye el
hibiscus y la okra, se ha usado tradicionalmente en Asia y Africa para la fabricación de cordeles.
Más recientemente, esta fibra ha generado interés en los Estados Unidos y otros países como
una fuente de fibras que se puede renovar anualmente y que se puede usar para una amplia gama de
aplicaciones, incluyendo pulpa y productos de papel así como en aislamientos, lechos para animales,
fibras y tejidos decorativos, absorbentes de aceite, y varios otros usos.
Uso en estructuras
De acuerdo a Birdair, la Kenafine®, que tiene un rango de durabilidad de cinco a seis años,
es especialmente apropiada para ser usada en estructuras temporales, como por ejemplo, en una
instalación para una competición olímpica o para un evento de corta duración.
Consistiendo de un tejido basado en kenaf/poliéster, revestido con una resina termoplástica,
la membrana no contiene cloruro polivinílico y por lo tanto no produce emisiones tóxicas cuando se
quema.
Todo el producto es completamente reciclable en productos de papel por medio de un proceso
basado en agua y que no utiliza substancias químicas, a diferencia de los procesos usados para la
elaboración de papel a partir de pulpa de madera.
Las funciones de la Kenafine son similares a las de las membranas de tejidos arquitectónicos
usadas tradicionalmente como coberturas tráslucidas y altamente resistentes a la humedad, y que
proveen un óptimo nivel de luz natural. El uso de esta membrana permite también que las estructuras
puedan recibir créditos de la agencia US Green Building Council Leadership en las categorías de
Diseño en Energía y Medio Ambiente.
“La Kenafine representa un paso único hacia adelante en la realización de un diseño
sostenible a través de la arquitectura diseñada para ser resistente a la tensión”, dijo Michele
Roth, gerente de mercadeo de Birdair, “La habilidad de ser capaces ahora de reciclar la membrana de
tejido en productos de papel hace que el diseño de resistencia a la tensión sea algo que pueda
mostrar responsabilidad hacia el medio ambiente, y al mismo tiempo le confiere al edificio una
apariencia estética agradable”.
Taiyo Kogyo
Taiyo Kogyo ha construido varias estructuras en Japón utilizando Kenafine, incluyendo
instalaciones que mostraron una versión inicial de esta membrana durante la Expo 2005, la
Exposición Mundial 2005, bajo el tema de “Sabiduría de la Naturaleza”, y estuvo instalada durante
seis meses en Aichi, Japón.
El primer producto fue diseñado para estructuras que serían usadas durante no más de un año.
Taiyo Kogyo se asoció después con el fabricante textil japonés, Sakai Ovex Co. Ltd., para mejorar
la durabilidad del material con el fin de que el mismo se pudiera usar durante más de cinco años,
agregando un revestimiento termoplástico a ambos lados del tejido.
La versión más reciente de Kenafine hizo su debut con ocasión del Sumit de G8 realizado en
Toyako, Japón, en el 2008. Allí se utilizó para cubrir la Galería Eco Centro Toyako Hokkaido – una
estructura de 800 metros cuadrados en la que se alojó la subsidiaria Hokkaido de la exhibición de
aprendizaje ambiental del Ministerio del Medio Ambiente de Japón.
Otros materiales
Otros materiales novedosos son el Vectran®, una fibra de poliacrilato de multifilamento de
alto rendimiento, fabricada por Kuraray America Inc., de Fort Mills, S.C., una sibsidiaria de
Kuraray Co. Ltd., de Tokio, Japón. Esta fibra de alta resistencia y baja elongación fue escogida
por la NASA para uso en las bolsas inflables en los aparatos de exploración de Marte.
Por otra parte, el Demron® es un producto, desarrollado por Radiation Shield Technologies
(RST), de Miami, que se usa para bloquear la radiación en los hospitales y otras instalaciones
médicas, siendo un producto liviano, flexible y que no es tóxico. Se puede usar en lugar de los
pesados delantales de plomo usados tradicionalmente.
Enero-Febrero de 2010