U
na idea destinada a superar los límites técnicos y de operación establecidos, y
finalmente una máquina y un proceso innovativo que se desarrolló por casi tres años con un alto
potencial de éxito en el mercado.
Hace alrededor de tres años, un conocido especialista contactó a la firma LAIP, de Prato,
para la realización de un proyecto verdaderamnte original. El especialista fue Leonardo Bianchi, de
la conocida compañía Bianchi L & G, una empresa con más de ochenta años de actividad pasados de
padre a hijo durante más de tres generaciones.
El principal campo de aplicación de la compañía ha sido durante mucho tiempo el lavado y
tratamiento con solventes para dar efectos de manipulación al tejido. La idea fue la de desarrollar
una máquina del tipo de flujo capaz de reemplazar exitosamente las lavadoras para el secado en seco
usadas previamente para el llamado proceso de “canastilla”.
El lanzamiento del modelo AIR Jet 2000, de LAIP, un modelo de aire/agua, sin problemas
mecánicos, llevó a Leonardo Bianchi a darse cuenta de que tal moderna y eficiente máquina podría
ser usada (con las debidas modificaciones y ajustes) también en este caso específico.
A su vez, los hermanos Becheri (los constructores) identificaron en esta creativa idea de su
socio la oportunidad de desarrollar un nuevo tipo de máquina apropiada para un proceso intermedio
(todavía no existente en el mercado) entre el lavado en canastilla y el lavado a lo ancho en
equipos convencionales.
Además, la meta fue la de obtener la versatilidad de procesamiento más alta posible con
relación a la capacidad de procesar tanto géneros de punto como materiales de lana, y ésto
independientemente del tipo del tejido en términos de composición (fibras), estructura, y pesos.
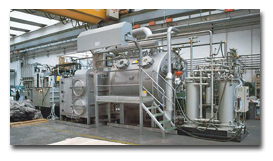
Vista de la máquina modelo
Wash & Dry, fabricada por LAIP
Desde el punto de vista de los últimos aspectos nombrados, el uso de solvente en el proceso
asegura una máxima eficiencia y buenos resultados técnicos, especialmente con materiales mezclados “
modernos” consistentes de materias primas naturales (lana, pelo fino, algodón, lino, etc) y fibras
artificiales y sintéticas, incluyendo los problemáticos componentes de elastano (Lycra, etc) para
los tejidos elásticos.
Y, finalmente, con esta máquina es posible también resolver la cuestión del consumo de agua,
así como de los costos del tratamiento de los efluentes. En realidad, el proceso del solvente se
efectúa en un ciclo cerrado, con una recuperación estimada en un 100% del percloroetileno usado.
Tecnologías de procesamiento
Bianchi L & G es un procesador a comisión, efectuando el lavado de los tejidos (sin
teñir y con hilo teñido) para remover los acabados, los aceites de mezclado, las siliconas del
lubricante, y otros productos aplicados a los materiales procesados provenientes de la cadena de
producción (hilatura, tejeduría, etc).
En el pasado, el uso de máquinas de canastilla convencionales (lavadoras industriales de
lavado en seco) permitían obtener, simultáneamente con el descrudado, también un cierto efecto de “
tacto”, generado por la acción mecánica en la superficie del sustrato textil siendo procesado.
Sin embargo, la efectividad de tales procesos es definitivamente menor que la obtenida con
solvente, ya que resulta en la presencia de varios porcentajes de los ya mencionados aceites,
siliconas, etc, en los tejidos tratados por el ciclo acuoso.
Es así que los socios Bianchi L & G y LAIP tuvieron la idea de diseñar una máquina
específica que permitiera obtener resultados perfectos en la remoción de dichos contaminantes,
reduciendo la carga en el personal, y obteniendo de todas maneras un cierto efecto cualitativo
(tacto) típico de los tratamientos en cuerda. Y fue así como se desarrolló la máquina Wash &
Dry.
Wash & Dry
La artesa de tratamiento de esta máquina consiste de una máquina de teñido en cuerda,
modificada apropiadamente para manejar solvente en lugar de agua. Por consiguiente, la bomba de
circulación y la tobera son substancialmente similares a aquellos de las máquinas construidas por
LAIP para el proceso clásico de teñido en pieza.
Obviamente, la tobera ha sido completamente rediseñada teniendo en cuenta que el peso del
cloruro es igual a 1.67 kg por litro de agua. Por lo tanto, para calcular el impulso del chorro en
el tejido también se tuvo que tener en cuenta este parámetro adicional.
El nuevo modelo Wash & Dry está equipado además con una tobera de aire (la cual se
derivó también de la experiencia obtenida por los hermanos Becheri con la AIR Jet 2000), que, al
final del tratamiento permite secar el material, con el tejido siendo transportado exclusivamente
por el flujo de aire caliente.
El ciclo de procesamiento consiste por lo tanto de dos fases distintas:
proceso de lavado del solvente, con el tejido siendo transportado por la bomba de
circulación de la máquina;
secado final con aire caliente, con el tejido siendo transportado por la Tobera AIR. La
instalación, cuya gran simplicidad es bastante aparente y relevante, es completada con una sección
integrada consistente de una unidad de Destilación, que opera de acuerdo a una innovativa
tecnología denominada “sistema sin agua”, desarrollada por una compañía socia de LAIP y cubierta
por una patente internacional.
En resumen, la destilación completa del solvente es realizada por unidades de refrigeración
(que bajan la temperatura a 15 °C bajo cero), con la posibilidad de una re-utilización casi total
del percloroetileno: resultados cercanos al 99%.
En relación con la tecnología de procesamiento, como regla general (que varía de acuerdo al
tipo de estilos que se están procesando), la misma comienza con la operación de lavado, efectuada a
la temperatura del salón y con una duración de 7-15 minutos, dependiendo del material. Esto es
seguido luego por el secado, con una duración de 30-60 minutos, dependiendo del tipo de tejido; y
el procesamiento termina con la fase de acondicionado/enfriamiento (5-10 minutos).
Testimonios
En el curso de más de 15 años de carrera profesional, el autor ha basado sus testimonios
sobre nuevos desa-rrollos no sólo en la información provista por el constructor de la máquina y con
la misma en operación comercial, sino también por el cliente o usuario de la máquina en cuestión.
En el caso de la máquina Wash & Dry, que entró en operación en la mencionada planta de
Bianchi L & G, ésta utilizó la máquina para el tratamiento de materiales sin teñir, asegurando
la remoción completa de aceites, acabados, siliconas, etc, comenzando con el tejido seco, y
entregando el material seco al final del ciclo. Las piezas de tela se pueden enviar luego al
departamento de acabado, o se pueden almacenar para ser acabadas después.
El procesamiento realizado en el modelo Wash & Dry ha provisto datos interesantes sobre
los efectos producidos por el lavado y secado en cuerda en la estructura del material procesado.
De hecho, parece que se facilita la compactacción del tejido de punto, con el encogimiento
del tejido variando entre un 5% y 18%, dependiendo de los parámetros específicos de los diversos
materiales (composición, peso, etc).
Con los tejidos de punto producidos con hilos teñidos se debe mencionar que, en el
procesamiento convencional, estos materiales deben ser sometidos primero a un proceso conocido como
“baño de encogimiento”, que incluye el lavado y suavizado de los tejidos, los cuales deben ser
luego hidroextractados y secados antes de pasar por sus tratamientos de acabado finales (perchado,
tundido, cepillado, etc).
Con el sistema Wash & Dry, la entera fase “húmeda” es eliminada, y el material es
procesado sin requirir nada de agua. Si es necesario, se puede añadir una pequeña cantidad de agua
(5-6 litros) para agregar un agente auxiliar suavizante al baño solvente, con el fin de suavizar el
tacto. El material, que es entregado seco al final del ciclo, se puede llevar entonces directamente
a la vaporizadora o a la rama tensora; o en otros casos, se transfiere a otras máquinas de acabado
superficial.
Data Técnicos
Versiones: 1- 2-3-4 cuerdas de tejido
Capacidad: desde 120 hasta 150 kg por cuerda
Ciclo: de 50 a 90 minutos (dependiendo del material)
Velocidad: de 50 a 300 m/min
Temperatura de operación de la Wash & Dry:
• de -15ºC a +80ºC para el proceso en húmedo
• de +15ºC a 130ºC para la fase de secado