MANCHESTER, Reino Unido- 8 de abril de 2025 – Las tecnologías de producción de fibras y tejidos -especialmente en el área de los refuerzos compuestos- han desempeñado hasta ahora un papel poco reconocido en el desarrollo de la industria de la Fórmula 1 en el Reino Unido, pero la British Textile Machinery Association (BTMA, Asociación Británica de Fabricantes de Maquinaria Textil) pretende cambiar esta situación.
El Valle del Automovilismo
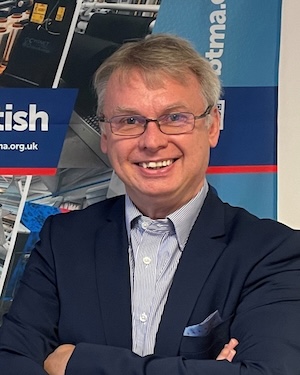
“Si hay algo que se le da bien al Reino Unido es la Fórmula 1, ya que siete de los diez equipos de F1 están situados a menos de una hora de distancia entre sí, en la región de las Midlands conocida como Motorsport Valley (El Valle del Automovilismo)”, explica Jason Kent, director general de la BTMA. “Todos ellos están vinculados a una red nacional de unas 4.500 empresas que participan en una industria automovilística y de ingeniería de alto rendimiento valorada en unos 9.000 millones de libras anuales y que da empleo a 40.000 personas. Esta red se nutre de los servicios de un número significativo de nuestras empresas miembros”.
“A excepción del motor, prácticamente todas las piezas de un coche de carreras de Fórmula 1 parten ahora de un textil, incluida la carrocería, los neumáticos y muchos de los últimos sistemas de combustible”, afirma Richard Kirkbright, director de proyectos de Roaches International, con sede en Leeds. “Esto ha influido en la evolución del sector automovilístico en general, además de la industria aeroespacial”.
Autos de Exhibición y Memorabilia
Aunque es más conocida por desarrollar sistemas de pruebas textiles, Roaches también ha suministrado a lo largo de los años autoclaves avanzados a la industria británica de los materiales compuestos, incluida una entrega reciente a Memento Exclusives, con sede en Northampton, especialista en la producción de coches de exhibición que trabaja directamente con la F1 y sus principales equipos.
Cada uno de los principales patrocinadores de equipos de F1 recibe uno o dos autos de exhibición para utilizarlos en exposiciones y en una amplia gama de actividades promocionales organizadas en torno al calendario de carreras. Estos autos no tienen motor y sus carrocerías pueden estar fabricadas con menos capas de fibra de carbono, pero por lo demás son idénticos a los últimos autos con los que compiten los equipos de F1.
Memento Exclusives tiene sus propias instalaciones de fabricación de piezas de fibra de carbono y la integración de autoclave Roaches ha ampliado significativamente sus capacidades en la producción de autos de exhibición.
Panaderos Maestros
“Los materiales compuestos sufren una metamorfosis en autoclave que los somete a procesos mecánicos y químicos”, explica Richard Kirkbright. “El aire y los volátiles atrapados se expulsan y las capas se consolidan bajo una presión precisa. A continuación, se introducen ciclos de calor, que curan los sistemas de resina y dan lugar a componentes impecablemente elaborados”. Los especialistas en autoclave son un poco como panaderos maestros, que saben exactamente cómo tratar sus ingredientes en cada etapa del proceso, para lograr el producto final deseado”.
“Autoclave Roaches nos permite ahora curar componentes de gran tamaño con un control total y conseguir una rápida rotación de las piezas, garantizando al mismo tiempo un acabado de la máxima calidad”, añade Terry Wasyliw, jefe de Construcción de Memento Exclusives.
La influencia de McLaren
McLaren, con sede en Woking (Reino Unido), fue el primer equipo de F1 que introdujo en 1981 un chasis fabricado íntegramente con compuestos de fibra de carbono, lo que supuso el pistoletazo de salida para la creación de una cadena de suministro global completamente nueva.
Este año, McLaren ha presentado una primicia mundial en la ingeniería de supercoches: la fibra de carbono de cinta rápida automatizada (ART por sus siglas en inglés) derivada de la industria aeroespacial, desarrollada en las instalaciones del Centro Tecnológico de Compuestos de McLaren (MCTC por sus siglas en inglés) en Sheffield. Se utiliza para crear las aletas delanteras activas del hipercoche W1, cuyo precio de salida es de 2,1 millones de dólares.
También se ha desarrollado para McLaren un componente del piso trasero en el marco del programa ASCEND, de 39,6 millones de libras, en el que han participado varios socios británicos, entre ellos Cygnet Texkimp, miembro de la BTMA.
Manipulación, Transformación y Descarbonización
Cygnet Texkimp suministra a la industria de los compuestos una amplia gama de máquinas de manipulación y conversión, entre las que se incluyen filetas a medida, máquinas de preimpregnado, revestimiento, corte y bobinado de filamentos.
Sus tecnologías se emplean en la construcción de componentes compuestos para la industria aeroespacial y automovilística, así como en la producción de cuerdas para neumáticos y, más recientemente, en la construcción avanzada de recipientes de almacenamiento de hidrógeno, que se consideran en gran medida el futuro de la propulsión de la F1, junto con baterías avanzadas para vehículos eléctricos.
Cygnet Texkimp lleva más de 20 años participando en la cadena de suministro de la F1 y la mayor parte de la fibra de carbono utilizada en el sector se ha procesado en una de sus filetas VHD. La empresa es también el mayor fabricante independiente de máquinas de preimpregnado del mundo y actualmente lidera el diseño y la construcción de las primeras líneas de investigación de fibra de carbono del Reino Unido para un proyecto dirigido por el National Composites Centre (NCC, Centro Nacional de Compuestos) con el fin de acelerar el desarrollo de fibras de carbono más sostenibles.
Además, Cygnet tiene licencia para diseñar y construir el sistema de reciclaje de materiales compuestos DEECOM® desarrollado por el nuevo miembro de la BTMA Longworth Sustainable Recycling Technologies, el primero de los cuales se ha puesto en marcha recientemente.
“La descarbonización es una de las principales prioridades de los fabricantes de todo el mundo”, afirma Luke Vardy, CEO de Cygnet. “En Cygnet Texkimp, estamos desarrollando la capacidad de procesar fibras técnicas de forma que permitan el aligeramiento, la energía de hidrógeno y la electrificación, reduzcan los residuos y revolucionen la gestión del final de la vida útil de los materiales compuestos y las piezas. En colaboración con nuestros socios industriales, estamos introduciendo en el mercado algunas de las nuevas tecnologías de procesamiento de fibras más innovadoras jamás desarrolladas para ofrecer beneficios reales que apoyen la agenda de la sostenibilidad”.
Preimpregnado
Otro nuevo miembro de la BTMA, Emerson & Renwick (E+R), especialista en tecnologías de impresión, conformado, vacío y revestimiento, también suministra tecnología para la producción de preimpregnados de fibra de carbono, que son rollos integrados de tejidos y resinas.
Su línea más reciente, de 1,7 metros de ancho, suministrada a un cliente en Italia, funciona a velocidades de más de 40 metros por minuto para el revestimiento de bandas o la consolidación de fibras y resinas preimpregnadas, o una combinación de ambos procesos. Se distingue por un revestidor de tres rodillos inversos de gran precisión para el procesamiento de resinas termoactivadas de alta viscosidad y permite el cambio automático de materiales de tejido sensible a tensión cero, con tres pinzas de calandrado de alta precisión con placas calientes/frías. Los múltiples sistemas de desbobinado y rebobinado para los pasos intermedios de laminación incluyen carga lateral y empalme de vuelta fiable y empalme a velocidad cero con un acumulador de banda para el rebobinado del producto principal.
E+R también ha formado parte de un consorcio que trabaja en el desarrollo de baterías de litio-azufre (Li-S) en el marco del programa británico Faraday Battery Challenge, dotado con 540 millones de libras. Una vez que sean comercialmente viables, las baterías de Li-S prometen proporcionar una densidad energética relativamente alta a bajo costo para los vehículos eléctricos sostenibles del futuro, empezando inevitablemente por la F1.
Fuertes Vínculos
“Además de nuestra potente base de empresas de ensayos y control textil, muchos otros miembros de la BTMA están trabajando en otros proyectos de F1 y compuestos avanzados”, afirma Jason Kent para concluir. “También estamos forjando fuertes vínculos con los principales centros de investigación del Reino Unido, como el Advanced Manufacturing Research Centre de la Universidad de Sheffield, el Northwest Composites Centre de Manchester, el National Centre for Motorsport Engineering de Bolton y el National Composites Centre de Bristol.
“La BTMA también se ha convertido recientemente en miembro asociado de Composites UK, porque este sector es el crisol de la innovación para los textiles del mañana”.
Publicado: 29 de abril de 2025
Fuente: Asociación Británica de Maquinaria Textil (BTMA)