INCA Renewtech fabrica nuevos compuestos con cáñamo, generando ganancias con sostenibilidad.
Adaptado de artículo escrito por Camille Sobrian Saltman
Poderosas fuerzas en el mercado han llevado a la industria textil a adoptar en sus productos materiales de origen doméstico más amigables con la protección del medio ambiente. Estas fuerzas incluyen regulaciones gubernamentales para reducir la contaminación de plásticos, atrapar carbono y obtener un mayor rendimiento en el ciclo de duración del producto.
También incluyen el enfoque de los inversionistas en iniciativas para el control del medio ambiente, sociales y de gobierno (environmental, social and gobernance, ESG, por sus siglas en inglés). Estas métricas se están usando ahora para medir el riesgo de las inversiones y determinar el valor de las corporaciones. De igual importancia es la creciente demanda de los consumidores por productos menos tóxicos y más sostenibles. Las compras del consumidor representan el 70% de la economía estadounidense y a medida que los clientes cambian sus patrones de compra las marcas mayores están realizando la transición al uso de productos reciclables.
Precio Afecta Adopción
Estas poderosas tendencias del mercado han llevado a innovaciones significativas en la química de polímeros bio-basados (o sea, basados en materias orgánicas), así como en materiales reforzados con fibras naturales. En la actualidad, muchos de los mismos productos que son sintetizados de moléculas de hidrocarbono derivadas de petróleo y gas natural se pueden producir con carbohidratos derivados de plantas de cultivo agropecuario.
Los beneficios potenciales de los materiales bio-basados ofrecen una gran promesa. Los productos basados en plantas atrapan carbono y no generan subproductos tóxicos y son mucho más fáciles de recuperar, reciclar, o incluso de ser usados como compuestos. Sin embargo, existen dos barreras significativas para su adopción en gran escala — el precio y el rendimiento.
Muchos biopolímeros, incluyendo el polihidroxialkanoate (PHA) y el ácido poliláctico (PLA) son más costosos que los incumbentes derivados de petróleo tales como polipropileno (PP) y polietileno (PE). Esto se debe principalmente a la economía de producción a escala o en gran cantidad. Los nuevos materiales tienen que competir con gigantescas compañías petroquímicas integradas verticalmente que han invertido billones de dólares en infraestructura de manufactura.
Por lo tanto, el precio está obstaculizando la formación de asociaciones para el desarrollo de mayores productos industriales, lo que es necesario para encontrar soluciones de elevado rendimiento. Hasta que los materiales bio-basados más sostenibles puedan competir en precio, los biomateriales seguirán siendo productos de nicho o especializados
Bio-masa de Cáñamo para Uso Industrial
La empresa INCA Renewable Technologies (INCA Renewtech), basada en Canadá, está tratando de resolver este penoso problema del mercado. En lugar de adquirir fibras naturales procedentes del extranjero, como hacen los competidores, la firma INCA está comprando biomasa de cáñamo de granjeros canadienses que crecen semillas de cáñamo para sacar proteína basada en plantas. La compañía procesa este producto renovable en una serie de productos exclusivos de alto valor para ser usado por mayores clientes industriales.
Al igual que la industria petrolera saca ventaja de su experiencia en exploración, extracción y manufactura de productos químicos para maximizar la recuperación financiera en cada barril de petróleo, INCA saca ventaja de la experiencia de la compañía en agronomía, procesamiento de fibras, innovación y manufactura de compuestos para maximizar la recuperación en cada bala de cáñamo.
Integración Vertical
Para lograr esta integración vertical, INCA va a construir dos plantas — una en Alberta, Canadá, dentro de un radio de 150 millas del cultivo de cáñamo; y una segunda planta en Bristol, Ind., dentro de un radio de 150 millas de los clientes en las industrias automotriz, de vehículos recreacionales (RV) y de productos para el consumidor.
El cáñamo se ha estado cultivando legalmente en las praderas canadienses durante más de 20 años, en donde se cultiva primariamente por su proteína basada en plantas. Los tallos restantes contienen algunas de las substancias naturales más fuertes en el mundo. Si son refinadas y manufacturadas de manera apropiada, las fibras de cáñamo pueden funcionar como un reemplazo directo de la fibra de vidrio en los materiales compuestos.
Las balas completas de cáñamo son desprovistas de la corteza, un proceso que separa mecánicamente la fibra basta exterior del corto núcleo interior, denominado “hurd”. La fibra basta se refina aún más para crear el material ultra limpio requerido por sus productos. En Alberta, el “hurd” se utiliza para manufacturar INCA BioBalsa™, un producto diseñado como un reemplazo directo para la madera de balsa usada en los botes y en las hélices de turbinas de viento.
La fibra basta refinada será enviada luego por ferrocarril a la segunda planta en Bristol, en donde será manufacturada en INCA BioPanels™ para la industria de RV; INCA Prepregs™ para la industria automotriz; e INCA BioPlastics™ para la industria de productos para el consumidor.
El origen y procesamiento doméstico del cáñamo reduce los costos logísticos y de material y reduce también los desafíos de la cadena de suministro, en comparación con la importación de fibras de yute, lino o kenaf del sureste de Asia, como hacen otros manufactureros de bio-compuestos.
Historia del Cáñamo
El cáñamo, o Canabis sativa L., fue uno de los primeros cultivos realizados por la humanidad, con fechas de uso que se remontan a más de 8.000 años. El cultivo del cáñamo comenzó en lo que es hoy China y se expandió rápidamente a través de Asia, Europa, Africa y más tarde Sudamérica. Además, hasta finales de 1800, la mayoría de papel en el mundo era producido de pulpa de cáñamo.
El cáñamo fue introducido originalmente a Norte América en 1606, cuando se cultivó para la elaboración de papel, correajes, aceite para lámparas y vestimentas. Sin embargo, a comienzos del Siglo 20 fuerzas poderosas se aliaron para hacer ilegal el cultivo de cáñamo, ya que fue visto como un competidor directo de la industria de la pulpa y del papel, y por DuPont, que inventó el nylon como un substituto basado en petróleo para los textiles de cáñamo.
Con el respaldo de poderosos cabilderos de la industria, el cáñamo fue incluido en la Ley 1938 de Drogas Narcóticas y Opio de Canadá, y en la Ley 1937 de Impuestos a la Marihuana en los Estados Unidos, lo que esencialmente acabó con la industria del cáñamo.
Pero el cáñamo está experimentando ahora un mayor resurgimiento en Norte América y alrededor del mundo. En 1998, fue legalizada la producción de cáñamo para uso comercial. En el 2020 ya había aproximadamente 53.000 acres dedicados al cultivo de cáñamo y se espera que esta cifra se va a expandir dramáticamente a medida que crece el mercado de fibras y proteínas basadas en plantas debido a algunas de las razones explicadas a continuación:
- El cáñamo se madura en tan solo 90 días y se puede cultivar con poco uso de agua y de productos químicos;
- Siendo una cosecha de rotación, el cáñamo rompe los ciclos de las enfermedades, y tiene una extensa área de raíces que sirven para la aireación del suelo;
- Tiene una producción de biomasa que es cuatro veces mayor que un bosque en una sola estación, en comparación con un árbol que requiere hasta 25 años para crecer; y
- Cada porción de la planta se puede comercializar, creando múltiples corrientes de ganancias.
Mercados que Pueden Usar Cáñamo
Desde la década de 1970, la industria de los vehículos recreacionales (RV por sus siglas en inglés), ha estado dependiendo de la madera dura de las selvas del sureste de Asia para construir paredes y techos. La resistencia de esta madera, su poco peso y su superficie suave hacen que este producto esté en gran demanda no solo para la construcción de RV sino también para remolques de transporte, muebles y paneles decorativos.
En el 2021, la industria de RV utilizó 620 millones de pies de planchas o paneles de madera dura. Los precios de esta madera se han elevado por las nubes, mientras que la calidad se ha reducido, y los manufactureros están buscando alternativas.
INCA ha desarrollado un producto de panel revolucionario hecho de una mezcla de fibras de cáñamo y un sistema exclusivo de resina termofijada. La compañía ha firmado un acuerdo de ventas exclusivo con Genesis Products Inc., de Elkhart, Ind., que diseña y manufactura una amplia variedad de productos para las industrias de RV, la construcción, el transporte, y los muebles. Genesis ha facilitado un acuerdo de desarrollo de productos con Winnebago para la producción completa de paneles de la compañía.
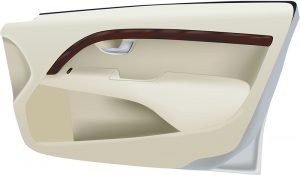
Industria Automotriz
La industria automotriz utiliza paneles con infusión de resina, llamados prepregs, para el moldeado de los componentes de accesorios interiores 3D, tales como paneles para puertas, parte posterior de los asientos, bandejas de paquete, y otros. Los prepregs pueden incorporar fibra de vidrio, fibras naturales o incluso fibras de carbono para reforzar la matriz de polímero térmico derretido. Los prepregs pueden venir en forma de paneles planos o de no tejidos como los producidos por las compañías FlexForm Technologies, en Elkhart, y Carver Non Woven Technologies, en Fremont, ambas en Indiana.
La industria automotriz fue una de las primeras en adoptar estos materiales prepregs debido a su bajo costo y alta resistencia en relación al peso, lo que resulta en un mejor rendimiento de la gasolina por millas recorridas y en una mejor seguridad para los clientes. Los fabricantes de automóviles calientan estos materiales prepregs en prensas calientes y las comprimen para hacer moldes 3D apropiados de acuerdo al uso final. Aunque los no tejidos también han sido de gran valor para la industria automotriz, los mismos dependen del uso intenso de costosas fibras naturales tales como yute y kenaf importadas del sureste de Asia.
A pedido del fabricante de automóviles Toyota, la firma INCA ha desarrollado una metodología para depositar una napa de cáñamo de varias capas y fibras de polímero, consolidando el material en una prensa de banda de acero para producir prepregs termo-formables para la industria automotriz. Estos prepregs serán más fuertes, mejorando la resistencia al impacto, así como más livianos, mejorando el número de millas recorrido por hora. Estos prepregs se pueden reciclar con facilidad en nuevos productos una vez que han alcanzado su duración útil en los automóviles.
Termoplásticos
Los plásticos son una industria multi-billonaria dominada por las compañías petroquímicas más grandes del mundo. Termoplásticos tales como PP, el polietileno de alta densidad (HDPE), y el cloruro de polivinilo (PVC) son usados en el empacado, en muebles, en pisos, en membranas para techos, en el interior de automóviles, en dispositivos médicos y en una cantidad innumerable de productos para el consumidor.
Su costo relativamente bajo, alta resistencia a la humedad, y su habilidad para ser calentado y formado usando equipos de inyección, compresión o extrusión hacen que el uso de plásticos sea muy común en el mundo moderno. Los principales productores de polímeros en el mundo son Dow Chemical, Lyondell Basell, Exxon Mobil, SABIC, INEOS y BASF.
La mayoría de los polímeros son derivados del petróleo o de gas natural. La extracción y el refinamiento de estas materias primas genera millones de toneladas de equivalente de bióxido de carbono (CO2), y los mismos contienen productos químicos tóxicos que se pueden acumular en los animales y en los seres humanos. Puesto que solo el 9% de los productos de plástico son reciclados, los mismos cubren la tierra y contaminan los océanos.
A menudo, los termoplásticos son combinados con fibras de vidrio para reforzar la matriz del polímero y mejorar las propiedades estructurales. Sin embargo, estos materiales incrementan el costo y el peso de los productos finales. La fibra de vidrio usa gran cantidad de energía para su manufactura y es también abrasiva para los equipos de procesamiento y difícil de reciclar una vez que el producto ha alcanzado su vida útil.
Los polímeros bio-basados representan un pequeño porcentaje de los millones de toneladas de plásticos fabricadas. Sin embargo, el mercado global de bio-plásticos y bio-polímeros está creciendo rápidamente. Las demandas del mercado incluyen productos sostenibles, regulaciones cada vez más estrictas y la preocupación del público relacionada con la contaminación causada por los plásticos.
Europa ha sido el mayor centro para la innovación de productos bio-basados y en la actualidad produce el 55% de todos los bio-polímeros, pero la capacidad de producción se está expandiendo ahora rápidamente hacia Asia y Norteamérica. Muchas de las compañías a la vanguardia de este cambio son empresas de bio-ciencia agrícolas o compañías petroleras que están haciendo la transición hacia productos químicos basados en plantas.
La firma Danimer Scientific, de Bainbridge, Ga., produce polihidroxyakanoates (PHA) usando aceites derivados de semillas de plantas tales como canola y soya. La compañía Total Corbion, basada en Holanda, opera una planta de producción de PLA de 75.000 toneladas al año en Tailandia y tiene planes para construir una segunda planta en Francia.
Por otra parte, la empresa NatureWorks LLC, de Plymouth, Minn., de propiedad de Cargill y PTT Global Chemical, tiene una refinería en Minnesota con la capacidad de producir 300 millones de libras de PLA al año usando alimentos de ganado basados en maíz. Aunque estos polímeros muestran una gran promesa, los mismos por lo general son más costosos que los polímeros basados en petróleo y tienen un rendimiento estructural inferior.
INCA ha desarrollado una novedosa metodología de manufactura para reemplazar la fibra de vidrio con fibras de cáñamo natural para uso como refuerzo en los compuestos poliméricos. En el proceso de INCA, la fibra de cáñamo es refinada de acuerdo a geometrías precisas y es luego mezclada con varios polímeros y aditivos bajo una presión y calor relativamente bajos, y esto preserva las propiedades estructurales de la fibra natural, así como las del polímero.
Los beneficios de los productos de INCA BioPlastics incluyen una reducción de costos y de peso, una mejor rigidez y resistencia al impacto, y un menor desgaste en los equipos de procesamiento. A diferencia de las fibras de vidrio, la fibra de cáñamo refinado es más amena a episodios de reciclado múltiple sin pérdida significante de las propiedades estructurales.
La empresa INCA realiza formulaciones de materiales que satisfacen las especificaciones de los clientes. Por ejemplo, una compañía quiere utilizar polipropileno recuperado para reducir los costos del producto y aumentar el contenido reciclado; mientras que otra firma puede especificar un polímero bio-basado tal como PLA o PHA para crear productos 100% bio-basados.
Estas formulaciones se crean en la forma de pellets o pelotillas de compuestos, que se pueden enviar directamente a los manufactureros para ser usados en sus equipos de inyección o en operaciones de moldeado por compresión, con pocas modificaciones a las líneas existentes, y los productos finales serán más fuertes, más livianos y menos costosos.
Hélices de Turbinas
El árbol de balsa es una especie de rápido crecimiento, nativa del sur de México y sur del Brasil. Aunque es clasificada como una madera dura, la balsa es excepcionalmente suave y de poco peso debido a que el tronco del árbol tiene grandes células que almacenan agua. Cuando se cortan y secan estas células grandes, las mismas retienen su estructura, dando a la madera una densidad excepcionalmente baja y una alta resistencia a la compresión. Como resultado de estas propiedades, la balsa se usa ampliamente como material de núcleo en las industrias automotriz, aeroespacial y marítima.
Recientemente, la balsa se ha convertido en uno de los materiales más usados en la construcción de hélices u hojas para turbinas de viento, ya que reduce el peso de la hélice e incrementa la rigidez de la misma, en especial en la sección de la raíz en donde las fuerzas mecánicas son más exigentes. Esto se logra colocando la balsa en el centro de la hélice y encapsulándola con fibra de vidrio recubierta de estireno para formar paneles de piel estirado.
Históricamente, la mayoría de la madera de balsa se extraía de las selvas de Ecuador, pero estas especies ya están casi extintas, creando impactos devastadores a los ecosistemas y comunidades indígenas. El 60% de la madera de balsa es ahora cultivada en plantaciones. Sin embargo, debido a que se requieren muchos años para cultivar palos grandes que produzcan madera sólida, la industria ha adoptado balsa de grano, o sea cortando los troncos a lo largo y rectificando las piezas rectangulares, y luego colocándolas juntas con pegante para formar una tabla. Esto ha añadido costos considerables al producto, reduciendo su consistencia y sus propiedades técnicas. Como resultado, muchos fabricantes de hélices están usando ahora PET de alta densidad y espumas de PVC en las puntas y secciones intermedias de las hélices, que es algo más costoso.
Los ingenieros de INCA han desarrollado una novedosa metodología para transformar el “hurd” de cáñamo refinado en un material parecido a la balsa, con alta uniformidad de compresión y una densidad de 10 libras por pie cúbico, lo que es un peso ideal para las hélices de turbinas. A diferencia de la balsa de madera, el material se puede formular para incrementar la resistencia a la humedad; y a diferencia de las espumas PET tiene la resistencia requerida para ser instalada en todas las secciones de la hélice de la turbina, incluyendo la sección de la raíz.
INCA ha firmado un acuerdo de desarrollo estratégico con la firma Gurit Services AG, de Suiza, para desarrollar y manufacturar BioBalsa. Gurit desarrolla y fabrica soluciones de compuestos avanzados para las industrias de energía de viento, aeroespacial y marítima. Su portafolio de materiales estructurales, prepregs, adhesivos, y servicios de ingeniería son reconocidos en todo el mundo.
Los clientes de Gurit están buscando activamente alternativas para materiales de núcleo que pueda ofrecer la resistencia compresiva de la balsa y satisfacer las metas de sostenibilidad.
Ciclo de Duración
INCA comisionó a la firma GreenStep Solutions Inc., basada en Canadá, una organización de investigación y certificación independiente, para realizar un Análisis del Ciclo de Duración Útil de los Productos fabricados por la compañía en comparación con alternativas convencionales que utilizan el Estándar de Protocolo de la Vida Útil y de Gases de Invernadero.
De acuerdo a la compañía, los resultados de este estudio mostraron lo siguiente:
- INCA BioPanels reduce las emisiones de carbono en un 76%, la producción de desperdicios en un 89% y el consumo de agua en un 82% en comparación con la madera dura luan extraída de la selva. Un metro cuadrado atrapará 4,27 kilogramos (kg) de CO2e.
- INCA BioPlastics, cuando se combina con polipropileno reciclado, reduce las emisiones de carbono en un 91%, la producción de desperdicios en un 64% y el consumo de agua en un 59%, en comparación con los plásticos reforzados con fibras de vidrio. Un metro cúbico absorbe 517,96 kg de CO2e.
- INCA BioBalsa tendrá un 164% menos impacto de carbono que el PET y un 107% menos que la madera de balsa. La producción resultará en un 93% menos de desperdicios que la balsa, y un 99.56% menos desperdicios que el PET, lo que también se traduce en un 93% menos de consumo de agua durante la manufactura. Un metro cúbico de BioBalsa absorbe 262,31 kg de CO2e.
La meta de INCA es ofrecer un triple beneficio para sus clientes — un mejor precio, rendimiento y sostenibilidad — con el fin de superar las actuales barreras para la adopción a escala industrial de los biomateriales.
Nota del editor: Camille Saltman es directora de marketing y sostentibilidad de INCA Renewtech.
Noviembre-Diciembre de 2022