E
n la edición anterior (Mayo/Junio) se publicó la
Primera Parte de este interesantísimo artículo para solucionar las variaciones
en el teñido de lote a lote. En esta edición, concluímos dicho artículo, y se incluyen también
algunas gráficas relevantes. Además, se hace una relación breve de las modernísimas instalaciones
inauguradas recientemente por Sarex Overseas en MIDC, Tarapur, India.
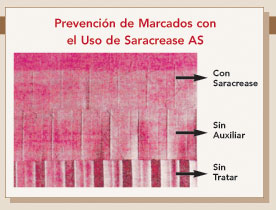
Parámetros de los procesos
La variación en los parámetros de los procesos pueden influenciar grandemente los resultados
obtenidos, como se describe a continuación:
• La inconsistencia en la relación de licor debida a la variación en el
tamaño del lote, la carencia de indicadores de nivel, así cuando no se tienen en cuenta el volumen
de solución de la sal, la solución del colorante y la solución del álcali cuando se calcula el
volumen total del licor.
• La falta de uniformidad de la longitud de la cuerda por tubo.
• Circulación de la cuerda demasiado lenta. Ideal: circulación de la cuerda
de 2-2.5 minutos.
• Adición/dosaje demasiado rápido de los colorantes y substancias químicas.
• Variación en los ingredientes de calentamiento y enfriamiento.
• Perfil ideal de tiempo/temperatura no seguido para el teñido y la
fijación.
• Dosamiento inexacto de colorantes y sal así como álcali, llevando a
inconsistencia.
• Relación de licor demasiado baja, lo que lleva a la precipitación del
colorante en tonos ya sea azules o de tonos obscuros.
• Rebaja en la eficiencia de la bomba de circulación, que no es notada.
• Paro de la máquina debido a enredos, o defectos mecánicos/electrónicos.
• Sobremanejo manual por el operario para compensar por demoras en el
procesamiento.
• Selección del programa de teñido equivocado.
• Sobremanejo de la máquina en el suavizador o en el agente de fijación del
colorante debido a la falta de disponibilidad de un carrito para el descargado.
• Rotura de la parte cosida debido a costura defectuosa.
• Rápido aumento de la temperatura en el blanqueado o en el teñido debido a
controladores defectuosos.
• Tiempos de blanqueado o de teñido más largos debido a baja presión del
vapor.
• Demora en el enjabonado o el enjuagado debido a la escacez de agua.
• Manchas de teñido debidas a la migración resultante de la demora en el
secado.
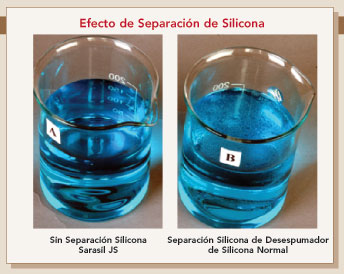
Papel administrativo
Basura adentro = basura afuera. Esto significa que si se empieza con entradas erróneas se
obtendrán resultados inaceptables.
Recomendaciones
Las recomendaciones principales son las siguientes:
1. Seleccione equipos de teñido en base a sus actuales y futuras
necesidades. No trate de copiar a su vecino o competidor, y no compre basado solamente en el
precio.
2. Estandarize o normalize su receta y proceso para obtener consistencia y
robustez. Discuta con sus proveedores, consultores y equipo técnico antes de seleccionar sus
productos y procesos.
3. Una vez que haga una lista corta de productos y proveedores no la
cambie, aún si otros proveedores le ofrecen productos equivalentes a costos menores. Recuerde que
el precio de la no conformidad es siempre más elevado que los ahorros en la compra.
4. Calibre y haga el mantenimiento de todos los instrumentos de medición.
Porque lo que puede ser medido, puede ser controlado.
5. Entrenamiento de trabajadores, supervisores, y personal técnico para
evitar errores inintecionados. Aprenda de los errores pero no repita el mismo error.
6. Fortalezca su laboratorio y establezca métodos estándares de control de
calidad para el análisis de las materias primas, el control de los procesos, y el control de
calidad de los productos acabados bajo el punto de vista de sus compradores. Asegure repetibilidad
y reproducibilidad de los resultados de los ensayos.
7. Interactúe con sus compradores y proveedores de manera regular para el
mejoramiento continuo de su trabajo. No descanse en sus laureles.
8. Efectúe la auditoría de procesos por parte de una agencia externa
especializada en el procesamiento.
9. Desapruebe los atajos o pasos acortados para ganar tiempo, pues esto
puede ser contraproductivo.
10. Seleccione personal con la actitud apropiada y la mente abierta, y no
sólo en base a cualificación y experiencia.
11. Mantenga un buen cuidado y mantenimiento. Un lugar para cada cosa y
cada cosa en su lugar, y sobre todo, preste atención especial al almacenaje de los colorantes y
substancias químicas, así como al área de trabajo alrededor de la máquina de teñir.
12. Utilize un programa de mantenimiento preventivo para que mantenga todos
sus equipos funcionando con la eficiencia requerida para obtener una producción óptima.
Recuerde la frase de Aristóteles: “Es posible fallar en muchas formas. Pero el tener éxito es
posible sólo en una forma — trabajo duro y perseverancia”.
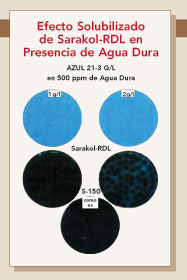
Modernas instalaciones
Aparte de la existente planta de producción de Sarex Overseas, dedicada a la manufactura de
productos químicos especiales e intermedios, la firma ha inaugurado una moderna planta en MIDC,
Tarapur.
Esta planta fue inaugurada por el Dr. Klaus Ruf, Director de Operaciones Técnicas de
Ciba-Basle, en Suiza, a principios de junio del presente año. Esta planta es una instalación que
usa el procesamiento por lotes y la mayoría de sus actividades son automatizadas por un Controlador
Lógico Programable (PLC).
Sin embargo, la característica básica y más importante de la planta es que ha sido diseñada
para la producción en volumen de un producto en particular, y además se puede usar para varios
propósitos y para la producción de productos especializados para varias industrias, tales como
textiles, plásticos, farmacéuticos, y otras industrias especializadas.
Las nuevas instalaciones están compuestas de cuatro unidades distintas: el bloque de
manufactura, el bloque de fuente de energía; el bloque de tanques, el bloque de tratamiento de
efluentes, y el tanque de agua y sistema de bombeado, en donde se llevan a cabo reacciones tales
como Sandmayer, y muchas otras.
De acuerdo al Dr. Naresh M. Saraf, Director de Sarex Overseas, la gran demanda proveniente de
varias industrias ha impulsado a Sarex a desarrollar y expandir sus capacidades de manufactura con
el fin de satisfacer las crecientes demandas.
Julio-Agosto de 2008