E
s difícil para el acabado textil el escapar la imagen de que es una industria que causa
emisiones. Sin embargo, hay maneras de reducir drásticamente las dificultades asociadas con los
procesos químicos en húmedo.
Dentro de la industria textil, el acabado textil es una de las principales fuentes de
emisiones. Como un abastecedor de modernas máquinas de acabado textil de alto rendimiento,
eficientes en el consumo de agua y energía, Benninger ha avanzado un paso más, ofreciendo ahora una
nueva gama de máquinas específicamente diseñadas para ahorrar aún más agua y energía.
La clave para esta gama de máquinas son los sistemas de filtración por diafragma, los cuales
permiten la recuperación del agua, materiales valiosos y la energía de desperdicio.
En el futuro, se espera que el agua se convertirá en un recurso cada vez más escaso y por
consiguiente más valioso. La demanda por agua está creciendo a más del doble de la tasa de
crecimiento de la población mundial. Durante los últimos 100 años, la población mundial se
incrementó tres veces, pero el consumo de agua se elevó en un factor de siete en el mismo periodo.
Se requieren alrededor de 2.500 – 3.000 litros de agua para la manufactura de una sola
camisa de algodón. La mayor parte de esta cantidad es requerida para el cultivo del algodón, pero
esto es seguido en segundo lugar por el proceso de acabado en húmedo.
Las primeras consecuencias de la escacez de agua ya se están sintiendo en la industria
textil. Así por ejemplo, nuevas compañías en China y la India no reciben aprobación para iniciar
sus operaciones a menos que demuestren pruebas convincentes de sus planes para resolver los
problemas relacionados con el consumo de agua. En Europa, muchas empresas se encaran al cierre por
la misma razón.
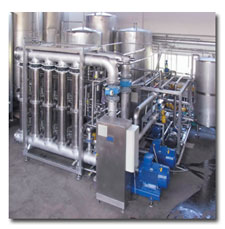
Figura 1: Esta planta de ultrafiltración, con un sistema de filtración por diafragma ,
fue diseñada para uso en la industria textil
Soluciones holísticas
La industria textil global se encara a un nuevo desafío. Como consecuencia de la escacez
global de agua y de energía, la industria necesita ahora métodos de producción que tengan en cuenta
la protección del medio ambiente. Desde mediados de la década de los 90, Benninger se alejó del
papel convencional de un fabricante de máquinas, y se estableció como un abastecedor de equipos de
procesos de acabado en húmedo para tejidos planos y de punto.
La compañía está ofreciendo ahora por primera vez soluciones holísticas para la industria
del acabado textil, bajo el lema de “manejo de recursos”. Estas soluciones representan una
producción textil sostenible y que es a la vez ética y apropiada para la protección del medio
ambiente. Parte de esta solución requiere la adopción de una actitud más cuidadosa en el uso de
agua, energía y productos químicos.
Además de las máquinas de acabado textil para tejidos planos y de punto, Benninger
suministra también los correspondientes sistemas de filtración por diafragma, los cuales se pueden
equipar con varias funciones que permiten los siguientes procesos:
• Separación del agua de los contaminantes introducidos por el proceso,
con el subsiguiente reciclado. Los contaminantes son concentrados hasta el punto en que no se
generan desperdicios líquidos (descarga cero). Al menos el 80% del agua de desperdicio es reusada
como agua de procesamiento.
• Recuperación de materiales reciclables del agua de desperdicio y el
reuso de estos materiales en el proceso (por ejemplo, encolante, soda cáustica, etc).
• Recuperación de la energía térmica.
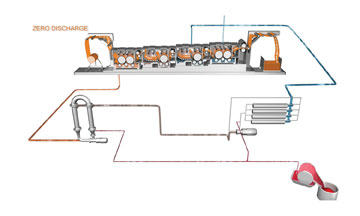
Figura 2: Diagrama de un sistema de cero descarga
Sistema de filtración por diafragma
En esencia, el sistema de diafragma de etapas múltiples consiste de una etapa de
ultra-filtración y una etapa de ósmosis en reversa más adelante. La etapa de ultra-filtración está
equipada con un diafragma de cerámica especial, el cual es usado para retener partículas y
componentes orgánicos de agua de desperdicio, de cadena larga, a temperaturas de hasta 95 °C.
Subsiguientemente, en el diafragma de ósmosis en reversa, los colorantes y las sales
disueltas son casi completamente separados del agua. Después, el agua de procesamiento tratada de
esta manera se puede reusar directamente en todas las áreas de la planta de acabado textil, sin
afectar adversamente la calidad del producto final.
Aunque este método se ha usado durante mucho tiempo en las industrias farmacéuticas y
alimenticias, es sólo gracias al uso de diafragmas de cerámica que son resistentes a los químicos y
a las altas temperaturas que este sistema se puede aplicar ahora a la industria textil, permitiendo
la filtración del agua desperdiciada de las plantas de producción textil, en procesos confiables y
continuos.
Con la ayuda de la ultra-filtración, es posible proteger la etapa de ósmosis en reversa
efectivamente contra la contaminación y asegurar así la fiabilidad operacional del sistema. Usando
una combinación de ultra-filtración y ósmosis en reversa, se pueden obtener tasas de recuperación
en exceso de un 80% del agua de desperdicio tratada.
Después del procesamiento con el sistema de filtración por diafragma, el agua de desperdicio
reciclada es incolora y puede tener valores COD de aproximadamente 100 – 300 mg/l y una
conductividad de alrededor de 100 µS/cm.
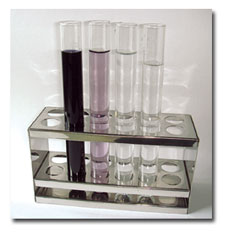
Figura 3: Muestras de agua de desperdicio de teñido tratada en sistemas de filtración por
diafragma.
1 = Agua de desperdicio
2 = Filtrado de la etapa de ultrafiltración
3 = Permeado de la etapa de ósmosis por reversa
4 = Agua fresca, por comparación
Desencolado
El agua de desencolado lleva una carga extremadamente elevada de COD. Al mismo tiempo, los
materiales reciclables se pueden recuperar usando encolante soluble en agua. Para hacer esto, se
requiere una planta de ultra-filtración con diafragmas de cerámica resistentes a la temperatura y
los productos químicos. Los resultados son sobresalientes:
• Reciclado de agua: 85 – 90%
• Reciclado de encolante: 75 – 85%
• Recuperación del calor: 70%
El agua de desperdicio proveniente del blanqueado del algodón tiene un alto valor COD debido
a las substancias orgánicas que acompañan al algodón. Esta agua es también generalmente de color
amarillo, de modo que es necesario una combinación de ultra-filtración seguida por la ósmosis en
reversa, para neutralizar el color. El concentrado no puede ser reusado, pero es subsi-
guientemente concentrado aún más y procesado en sólidos o quemado. Los resultados en este caso
también son sobresalientes:
• Reciclado de agua: 80 – 90%
• Recuperación del calor: 70%
El proceso de mercerizado genera agua de lavado con una alta concentración de soda cáustica,
de alrededor de 60 g/l. La ultra-filtración es usada inicialmente para limpiar y concentrar la soda
cáustica en el agua de lavado y reducir su volumen. Después de ésto, la soda cáustica es
concentrada a 35 – 42°Be usando métodos de evaporación convencional, lo que permite que la soda
cáustica se pueda reutilizar en la planta de mercerizado.
Puesto que los métodos de evaporación convencional requieren un intenso uso de energía, es
una buena solución concentrar el agua de lavado antes de la ultra-filtración. Los ahorros
potenciales después de esta etapa son enormes:
• Reciclado de soda cáustica: 75 – 80%
• Reciclado de agua: 80 – 85%
• Recuperación del calor: 70%
El agua de desperdicio proveniente del proceso de teñido tiene una fuerte coloración y un
alto contenido de electrólitos, de manera que se requiere una combinación de ultra-filtración y
ósmosis en reversa. Nuevamente, se obtienen excelentes resultados en este caso:
• Reciclado de agua: 80 – 90%
• Recuperación del calor: 70%
Proceso de concentrados
Como se describió anteriormente, los concentrados generados en los sistemas de diafragma se
pueden reusar solamente para el reciclado de encolantes y la recuperación de la soda cáustica. En
todos los otros casos, los concentrados son licores altamente contaminados, y por lo tanto no es
posible descargar estos concentrados en ríos o lagos.
Para una operación de la planta libre de agua de desperdicio (descarga cero), todos los
concentrados deben ser engrosados y solidificados. Los concentrados engrosados se pueden
solidificar aún más, por ejemplo, usando técnicas de evaporación, o pueden ser quemados.
Las soluciones potenciales para las plantas de acabado de tejidos de punto están basadas en
los mismos principios usados en el acabado de tejidos planos (no desencolado). Sin embargo,
hay que hacer mucho más para asegurar que los métodos usados en el acabado de tejidos de punto se
mantengan a la par, particularmente debido a que las plantas usan a menudo procesos de agotamiento
en equipos a chorro o de flujo suave. Agua y consumo de energía asociado con este sistema es 2 – 3
veces más elevado que un sistema moderno.
Costos
Las plantas de filtración por diafragma funcionan de manera completamente automática. Todos
los parámetros de operación relevantes, tales como la temperatura, la tasa de flujo, la presión de
operación, etc, son controladas por medio de un PLC. Los procesos de flujo posterior y procesos de
limpiado comienzan automáticamente.
La inversión inicial para los diafragmas de cerámica es más elevada que para los diafragmas
de polímero. Gracias a su alta resistencia a la temperatura y a la resistencia química, su duración
oscila entre 5 y 10 años (nota: Van Clewe /D > 8 años). Los diafragmas convencionales de
polímero se usan en la etapa de ósmosis en reversa, y estos tienen una duración de 2 – 3 años.
Los costos de operación para un sistema de diafragma de dos etapas son de alrededor de 0.60
euros/m3, lo que incluye tanto los costos de inversión inicial como los costos de operación de la
planta. El periodo de amortización para un sistema de diafragma para agua de desperdicio textil es
de alrededor de 2 – 3 años para el agua de reciclado y para la recuperación del calor. Si el
sistema se usa también para el reciclado de encolante y para la recuperación de soda cáustica,
entonces el periodo de amortización es de alrededor de 1 – 2 años.
Las opciones pasivas son:
• Cambios en el proceso, por ejemplo, teñido continuo en lugar de
tratamientos a chorro
• Optimización de los procesos y recetas existentes
• Uso de tecnologías de lavado y acabado altamente eficientes.
La lista de opciones activas incluyen el uso de tecnología de filtración para la
recuperación del agua, la energía y los materiales reciclables del agua de desperdicio de las
plantas de acabado en húmedo. Por primera vez, los diafragmas de cerámica usados en la etapa de
ultra-filtración permiten la operación confiable y continua para el tratamiento del agua de
desperdicio de los procesos de acabado textil. Al mismo tiempo, estos métodos actúan también como
un amortiguador protectivo para la etapa posterior de ósmosis en reversa, la cual es usada para la
filtración de colorantes y electrólitos disueltos y no generan desperdicio.
Septiembre-Octubre de 2008