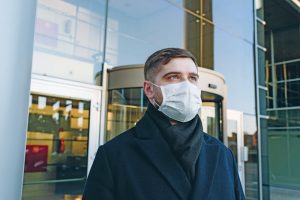
Las innovaciones en la fabricación brindarán una protección más confiable, adaptable frente a la pandemia.
Por Behnam Pourdeyhimi, Simon Schick y Robert Groten.
La Organización Mundial de la Salud (OMS) publicó recientemente los hallazgos de su investigación sobre lo que salió bien y lo que salió mal mientras el mundo se enfrentaba a la pandemia de coronavirus. Un informe de 86 páginas señaló que había “eslabones débiles en cada punto de la cadena de preparación y respuesta”. Un panel de 13 miembros designado por la OMS calificó la pandemia de COVID-19 como un “desastre prevenible”.
Algunas de las recomendaciones resultantes de la investigación incluyeron:
- Crear un sistema mejorado de vigilancia y alertas de enfermedades, a una velocidad que pueda combatir virus como el que causa el COVID-19, junto con la autoridad para que la OMS publique información y envíe misiones de expertos de inmediato.
- La capacidad de producir vacunas, diagnósticos, productos terapéuticos y suministros y asegurar su entrega rápida y equitativa como bienes comunes esenciales globales.
- La producción y el acceso a las pruebas y tratamientos de COVID-19, incluido el oxígeno, deben escalarse urgentemente a los países de ingresos bajos y medianos.
La vicepresidenta Kamala Harris y la embajadora de los Estados Unidos, Linda Thomas-Greenfield, abrieron recientemente un diálogo sobre la preparación para una pandemia con el objetivo de aprender las lecciones aprendidas del COVID-19, que fue organizado conjuntamente por Argentina, Noruega, Japón, Sudáfrica y Estados Unidos.
“La morajela del año pasado es clara: el mundo apenas resistió esta pandemia”, dijo Thomas-Greenfield al dirigirse al grupo global compuesto por líderes políticos, de salud pública y de organizaciones no gubernamentales. “Debemos estar preparados para la próxima. No podemos seguir invirtiendo insuficientemente, después de brotes, epidemias y ahora una pandemia, en nuestra capacidad para prevenir, y responder a las amenazas de enfermedades infecciosas”.
Tengamos en cuenta que la OMS no aborda específicamente los desafíos con equipo de protección personal (EPP), sino que se centra en los desafíos con productos terapéuticos, entre otras soluciones. El segundo punto anterior es un punto clave: tener la capacidad de producir lo que se necesita rápidamente y entregar estos suministros de manera global y equitativa.
Cuando se trata de productos como las mascarillas, por ejemplo, es difícil producirlos rápidamente y distribuirlos de manera equitativa en los países de ingresos bajos y medios. Se necesita un cambio de paradigma y las mascarillas de tela no son la solución.
Antecedentes
Cubrirse para proteger la boca y la nariz se remonta a principios del siglo XX. En 1897, Carl Friedrich Flügge discutió la posibilidad de infecciones por gotitas originadas por la tos y, curiosamente, identificó por primera vez la importancia del distanciamiento social1,2. La transmisión aérea del cólera, la peste y la meningitis cerebroespinal se discutieron reconociéndose la importancia de usar un “vendaje para la boca”, una sola capa de gasa de algodón1. Posteriormente, las mascarillas de algodón se utilizaron ampliamente durante la pandemia de gripe española de 1918-1920.
En contraste con esta simple tecnología basada en tela, los respiradores y mascarillas actuales se centran en dos tecnologías clave: fibras finas meltblown (soplado en fundido); y una carga electrostática. El meltblowing en sí se remonta a 1941, cuando el proceso fue inventado3. Inmediatamente se reconoció que el meltblowing puede producir fibras muy finas en comparación con el hilado en fusión tradicional de fibras4. La fusión por soplado es un proceso muy económico a gran escala que crea diámetros de fibra que van desde submicrones hasta unos pocos micrones.
La carga electrostática mejora la eficiencia de interceptación de partículas de tales fibras mientras produce una caída de presión general significativamente menor, una medida de la resistencia que encuentra el aire cuando fluye a través de la mascarilla, que debe ser lo suficientemente baja como para que el esfuerzo requerido para respirar sea lo más normal posible.
Otras tecnologías críticas se centraron en garantizar que la densidad de carga fuera inicialmente alta y, lo que es más importante, estable. La primera mascarilla “moderna” se introdujo en 19675, mientras que el primer respirador se patentó en 1976. Un desarrollo crítico fue la aplicación de carga electrostática a los tejidos meltblown en 19806. Pronto siguieron las patentes clave que condujeron a los respiradores N95 ampliamente utilizados actualmente. La primera patente de este tipo se otorgó a 3M Co., con sede en Saint Paul, Minnesota, en 1980, cuando se cargó una estructura fundida por soplado para formar un filtro electrostático de alta eficiencia7. En 1985, 3M desarrolló el primer respirador moderno moldeado en forma de copa8.
Filtración ideal
Los aerosoles son una suspensión de partículas sólidas o líquidas en un gas que varían en tamaño de 2 nanómetros (nm) a 100 micrómetros. Los bioaerosoles son aerosoles de origen biológico, incluidos virus, bacterias y hongos. Un filtro ideal elimina solo las partículas de aerosol no deseadas del aire y lo hace sin crear una gran caída de presión. Hay cuatro mecanismos primarios de filtración de aerosoles9 (ver Figura 1).
La corriente de aire gira a medida que se mueve alrededor de las fibras. Las partículas grandes quedan atrapadas por impacto inercial. Las partículas grandes tienen una alta probabilidad de impactarse con una fibra porque la inercia hace que se desvíen de la línea de la corriente. El impacto inercial es para micropartículas grandes y se vuelve importante a velocidades altas y medias. Las partículas muy pequeñas también tienen una alta probabilidad de chocar con una fibra debido al movimiento browniano. El movimiento browniano se produce cuando las partículas colisionan con moléculas de gas (aire) que son mucho más pequeñas que las partículas. Esto conduce a un movimiento caótico, desordenado y abrupto, que conduce a la difusión. El mecanismo de captura de partículas de menos de 100 nm se debe principalmente a la difusión.
Sin embargo, las partículas de mayor tamaño, desde aproximadamente 100 nm hasta 400 nm, con aproximadamente 300 nm representan el tamaño de partícula más difícil de capturar, normalmente siguen las líneas de flujo de aire y son las más difíciles de atrapar. El mecanismo de captura se debe a la interceptación, ya que las partículas pueden ser interceptadas por una fibra. Es aquí donde la atracción electrostática se vuelve importante. Las partículas con carga opuesta son atraídas por una fibra cargada. Este mecanismo de recolección no favorece particularmente un cierto tamaño de partícula, pero es más significativo para las partículas más difíciles de capturar.
El tamaño de la fibra se vuelve crítico para el mecanismo de captura de interceptación. Si las fibras son del mismo tamaño o más pequeñas, tienden a ser más efectivas para interceptar las partículas. Esto, junto con una alta atracción electrostática, conduce a una alta eficiencia de recolección de filtración en los respiradores y mascarillas médicas actuales que responden a las estructuras cargadas meltblown.

Las mascarillas de tela producidas a partir de fibras textiles regulares emplean fibras mucho más grandes, más de 15 micrones en la mayoría de los casos, carecen de carga electrostática y las estructuras crean grandes huecos o agujeros. Estos huecos conducen a áreas localizadas que tienen una caída de presión mucho menor y, por lo tanto, la corriente de aire fluirá naturalmente a estas áreas, llevando las partículas de aerosol a través de la estructura. Estas mascarillas casi no ofrecen protección respiratoria. Sin embargo, son útiles para reducir el número de partículas expulsadas por el usuario, lo que puede resultar en la reducción de la propagación de un virus aunque no ofrezcan mucha protección al usuario. Por lo tanto, las mascarillas de tela son útiles como un medio de control de la fuente para usuarios al reducir el número de gotas y aerosoles expulsados de la nariz y la boca del usuario al aire10.
Retos durante el Covid-19
Los filtros de la mascarilla están hechos casi exclusivamente de materiales no tejidos de polipropileno (PP) meltblown (MB) cargados electrostáticamente. Los filtros MB tienen fibras en el rango de 0,5 a 5 micrones de tamaño y, por lo tanto, son frágiles y deben protegerse con capas de PP spunbond (SB) compuestas por fibras más grandes, de 15 a 25 micrones, que brindan protección mecánica al filtro con capa MB.
La cadena de suministro general consta de:
- Fabricantes de tejidos MB;
- Fabricantes de telas SB;
- Convertidores de mascarillas que ensamblan las telas MB y SB en mascarillas.
El doble desafío al que se enfrentó en Estados Unidos y en todo el mundo durante la pandemia de Covid-19 fue la producción limitada de MB y la falta de infraestructura necesaria para convertir los tejidos en mascarillas.
Las instalaciones de producción de MB y SB siempre se construyen a medida, son grandes y costosas y requieren una infraestructura significativa. El tiempo de espera para establecer nuevas capacidades suele ser mayor a 10 meses a un costo de más de $10 millones para una máquina pequeña de 1,6 metros de ancho. Por lo tanto, incluso en las regiones de altos ingresos de Norteamérica y la Unión Europea, las plantas no se podrían desplegar más rápido. En otras regiones del mundo, sería imposible acelerarlas rápidamente, y es por eso que debe haber un cambio de paradigma. Por el contrario, la conversión de mascarillas está más disponible, es relativamente económica y no requiere una infraestructura especial.
Las máquinas MB son mucho más caras que la suma de sus componentes. Los conocimientos técnicos de ingeniería y, en algunos casos, la propiedad intelectual, crean barreras de entrada. Meltblowing, por ejemplo, es un proceso bastante simple. La clave de la tecnología es la punta de la matriz que controla la uniformidad de las fibras producidas. El resto de los componentes están listos para usarse. Sin embargo, la industria de los no tejidos se basa en
grandes volúmenes, alta velocidad, bajos costos de producción y automatización. Es por eso que la industria de los no tejidos continúa liderando el mundo en productividad e innovación.
Lo que se necesita para productos como mascarillas y respiradores es una solución diferente. La conversión de la máscara también es un proceso totalmente automatizado, y los requisitos de ancho oscilan entre 19,5 centímetros (cm) y 32 cm como máximo. Hay que tener en cuenta que la conversión de mascarillas no requiere una infraestructura especial como, por ejemplo, un gran espacio de bahía. Si se diseñó una máquina MB que solo tiene, digamos, 40 cm de ancho, el proceso seguirá siendo lo suficientemente rápido como para suministrar muchas máquinas de conversión de mascarillas, mientras que los costos serán bajos y no se necesitará una infraestructura especial. Tomemos, por ejemplo, la línea piloto de Biax Fiber Film que mide 15 pulgadas (38 cm) de ancho. Con
algunos cambios menores puede convertirse en una máquina de producción de filtros de
supermascarilla que también se puede colocar con el equipo de conversión de mascarillas. Hay otros ejemplos de líneas de menor impacto que se utilizan principalmente como líneas piloto. Estos diseños se pueden replicar y reproducir fácilmente según sea necesario.
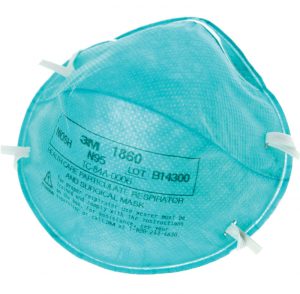
(Brian McGowan/Unsplash)
Falta de Técnicos, Disponibilidad de Equipos
Otro desafío importante durante la pandemia fue la falta de conocimientos técnicos. Las estructuras meltblown requieren aditivos como potenciadores de carga y estabilizadores de carga. Si bien algunos masterbatches (lotes maestro) están disponibles comercialmente, algunos funcionan y otros no. Además, si bien la maquinaria meltblown está completamente automatizada, la tela resultante se ve afectada por las variables del proceso y, por lo tanto, se requiere un enfoque de prueba y error para establecer las condiciones del proceso que conducen a las características de rendimiento deseadas. Si bien había empresas en Norteamérica que producían otros productos meltblown, cambiar a medios filtrantes no fue una tarea sencilla.
Otro desafío al que se enfrentó en Norteamérica fue que nadie producía maquinaria de conversión de mascarillas antes de la pandemia. Esto no se debió a una falta de experiencia o capacidades, sino más bien fue algo impulsado por la simple economía. Las máquinas fabricadas en Asia se vendieron por tan solo $30.000 hasta $120.000 y podrían entregarse en unas pocas semanas. El costo de los componentes en Norteamérica sería más alto que el del producto terminado y dado que las máquinas tienen un aspecto similar y funcionan de manera similar, la tendencia ha sido inclinarse hacia la maquinaria de fabricación asiática. La falta de soporte técnico, un suministro inadecuado de piezas y la falta de confianza de la maquinaria, a menudo provocaban retrasos y costos de producción mucho más elevados.
Unos dieciséis meses después, la situación ha cambiado. Hay algunas instalaciones nuevas para el meltblowing y, según la Asociación de la Industria de No Tejidos (INDA por sus siglas en inglés) con sede en Cary, N.C., hay más de 70 empresas que han invertido en equipos de conversión de mascarillas desde el comienzo de la pandemia. Sin embargo, gran parte de la nueva maquinaria es para la producción de la clásica mascarilla quirúrgica de tres capas. Con las mascarillas quirúrgicas asiáticas baratas inundando el mercado durante los últimos 6 meses, es cuestionable si muchas de las empresas que hicieron inversiones serán capaces de competir. Esto, a su vez, generará desafíos para la capacidad de MB instalada.
Hay muchas menos máquinas N95 instaladas. Además, las mascarillas médicas y los respiradores están regulados por el Instituto Nacional de Seguridad y Salud Ocupacional (NIOSH por sus siglas en inglés), la Administración de Drogas y Alimentos de los Estados Unidos (FDA por sus siglas en inglés) y la Administración de Salud y Seguridad Ocupacional (OSHA por sus siglas en inglés), y otra barrera para ingresar al mercado actual es el largo plazo de entrega requerido para la certificación.
Muchas empresas han estado esperando la certificación durante muchos meses y la fila no se está acortando. La certificación también requiere el desarrollo de un sistema de gestión de la calidad, como la certificación de la Organización Internacional de Estandarización (ISO por sus siglas en inglés) o las buenas prácticas de fabricación (GMP por sus siglas en inglés), barreras adicionales para la entrada al mercado.
¿Qué Pasará con la Próxima Pandemia?
No se trata de si ocurre otra pandemia mundial, sino de cuándo. En ausencia de políticas que fomenten la fabricación nacional de EPP y otros productos críticos, la situación de escasez en Estados Unidos probablemente no será diferente. En ausencia de una manufactura democratizada, los países de bajos ingresos seguirán estando en desventaja.
El status quo de la fabricación de EPP no está lo suficientemente avanzado como para proteger definitivamente a Estados Unidos del próximo brote viral. Otras innovaciones de fabricación son el camino a seguir hacia una protección más confiable, asequible y adaptable. Las mascarillas de tela no serán la solución y se regularán quizás usando la nueva ASTM 3502 o su equivalente.
El Nonwovens Institute de Raleigh, N.C., y sus socios están desarrollando estrategias de fabricación y programas educativos para ayudar a establecer estándares mínimos definitivos para la fabricación que serían escalables y fácilmente reproducibles.
Referencias:
1 Flügge, C. Ueber Luftinfection. Zeitschr. f. Higiene. 25, 179–224 (1897). https://doi.org/10.1007/BF02220473
2 C. Flügge, La propagación de la tisis a través de esputo polvoriento y gotitas que se rocían al toser, Journal of Hygiene and Infectious Diseases volumen 30, páginas 107 – 124 (1899).
3 JG McCulloch, La historia del desarrollo de la tecnología de soplado en fusión International Nonwovens Journal, 1999.
4 Wente, V.A., Laboratorio de Investigaciones Navales, Informe 4364, Fabricación de Fibras Superfinas. Mayo 25 de 1954.
5 Patente de Estados Unidos 3.333.585
6 Patente de Estados Unidos 3.971.373A
7 Patente de Estados Unidos 4.215.682A
8 Patente de Estados Unidos 4.536.440ª
9 Pourdeyhimi, Schick y Groten, La Eficiencia de Filtración de los Textiles de una sola Capa para la Protección Respiratoria, The Journal of Science and Medicine, Vol. 3 No. 2 (2021).
10 Pourdeyhimi, Schick y Groten, Efectividad Respiratoria de las Mascarillas de Tela, The Journal of Science and Medicine, Vol. 2 No. 4 (2021).
Nota del editor: Dr. Behnam Pourdeyhimi es decano asociado para Investigación y Extensión de la Industria; William A. Klopman es distinguido profesor de materiales, profesor de Ingeniería Química y Biomolecular e Ingeniería Biomédica y director ejecutivo en The Nonwovens Institute (NWI), Wilson College of Textiles en la Universidad del Estado de Carolina del Norte, Raleigh, C.N.; Simon Schick, estudiante de maestría en NWI y en el estado de Carolina del Norte; y Robert Groten, profesor de la Universidad de Ciencias Aplicadas Hochschule Niederrhein, con sede en Alemania, y profesor adjunto en el estado de Carolina del Norte.
Julio-Agosto de 2021