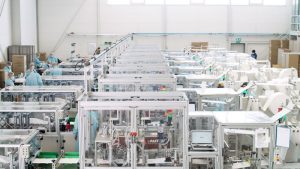
Autefa y Emerson aportan tecnología a la línea de producción de respiradores instalada por Univent Medical.
Didier Perret
La pandemia del Covid-19 que se desató simultáneamente en todo el mundo a principios del 2020, ejerció una tremenda presión en los gobiernos, industrias, organizaciones de la salud, y otros campos, para encontrar la manera de proteger al público contra la pandemia.
El día 9 de abril del 2020, el gobierno federal de Alemania estableció un comité laboral bajo la dirección del Ministro Federal para Asuntos Económicos y Energía (BMWi), con el fin de coordinar la producción expandida de equipos de protección personal, así como de pruebas y equipos de pruebas, e ingredientes activos para realizar pruebas de Covid-19 en Alemania y la Unión Europea (E.U.).
En poco tiempo, el comité laboral de la BMWi desarrolló estimados con los cuales calculó que Alemania necesitaría una producción anual de 750 millones de respiradores filtradores tipo FFP2 y FFP3, y 1.750 millones de mascarillas faciales médicas para satisfacer el nivel agregado de la demanda. Poco después, el gobierno federal alemán buscó hacer contratos con los fabricantes de respiradores y mascarillas para cumplir con sus metas ambiciosas.
Contrato con el gobierno
La empresa Univent Medical, de Schwenningen, Alemania, un fabricante de mascarillas respiratorias de alta calidad, recibió un contrato que requería el aumento dramático de su producción de respiradores Atemious Pro FFP2.
Cuando recibió esta enorme propuesta del gobierno, Univent buscó la compra de nuevas líneas de manufactura automatizadas para producir 1 millón de respiradores FFP2 a la semana. La firma Autefa Solutions Switzerland AG, de Frauenfeld, Suiza, tomó un concepto de máquina de producción existente y lo transformó para cumplir con las regulaciones de seguridad europeas.
Este concepto usaba inicialmente soldadores ultrasónicos, fabricados en Asia, que eran de calidad mediana. Aunque estos soldadores podían soportar tasas de producción ordinarias en las máquinas fabricantes de mascarillas, no tenían las características requeridas para fabricar y sostener una calidad superior a máximas tasas de producción.
Un problema que causaba preocupación en particular era su consistencia y repetibilidad en el bondeado de las láminas de mascarillas de cuatro capas con la resistencia requerida a las mayores velocidades de producción requeridas.
La compañía Autefa se puso en contacto con Emerson, fabricante de equipos de soldadura de plástico ultrasónicos Branson™, para que la firma recomendara los tipos de soldadores que podrían brindar la potencia, la calidad y la velocidad requerida por Univent.
Emerson recomendó el retro-equipado de cuatro estaciones de soldadura ultrasónica, con equipos ultrasónicos Brandon DCX Series de alto rendimiento y alta potencia, así como nuevas herramientas de producción ultrasónico optimizadas. Las herramientas de soldadura incluyen nuevos convertidores, boosters, y sonotrodos de soldado especializados para cada tarea de soldadura.
Los equipos de herramientas son fabricados y mantenidos por el representante local de Emerson en Suiza, Pascal Baechtiger. Aceptando el consejo de Autefa, Univent aprobó el retro-equipado de los equipos. Emerson cumplió con los pedidos — para 32 equipos de soldadura de potencia ultrasónica y las herramientas necesarias — en menos de seis semanas. Luego de la entrega de los soldadores, los representantes de Emerson ofrecieron apoyo técnico en el sitio a medida que el personal de Autefa completaba el retro-equipado de los soldadores.
“La experiencia y responsabilidad del equipo de soldadura ultrasónica Branson, de Emerson, permitió que Autefa pudiera comenzar rápidamente el programa de reconstrucción de los equipos, sin una larga curva de aprendizaje”, dijo André Imhof, CEO de Autefa Solutions Switzerland AG. Cuando las máquinas de manufactura de mascarillas reconstruidas resumieron su producción, Univent sintió el impacto ahí mismo. Thomas Vosseler, director y co-propietario de Univent, declaró: “Gracias a la responsabilidad y al rendimiento de los nuevos equipos de potencia Branson y las herramientas de soldadura, cada una de las ocho máquinas de producción han incrementado su velocidad y producción con una alta confiabilidad, permitiéndonos aumentar la producción a 4.5 millones de respiradores Atemious Pro FFP2 cada mes”.
Cuando se trata del mejoramiento de la calidad y de la velocidad de producción, cada detalle es importante. Así por ejemplo, dos de las cuatro estaciones de soldadura ultrasónica en cada máquina manufacturera de mascarillas son dedicadas a adherir las orejeras elásticas, lo cual es esencial para asegurar un ajuste confortable y a prueba de aire. La nueva tecnología Branson adhiere al mismo tiempo las orejeras derecha e izquierda y en menos de un cuarto de segundo. Y usando el “modo de energía” del equipo de potencia de soldadura Branson DCX, las soldaduras son perfectamente confiables — un incremento substancial tanto en la calidad como en la velocidad en comparación con otros sistemas de soldadura más elementales.
Vosseler calcula que el uso de equipos de soldadura Branson de alta calidad, “permite un 95% de eficiencia de las líneas automatizadas existentes, en comparación con menos de 60% de eficiencia de producción observada generalmente con los equipos de soldadura ultrasónica de nivel inferior”. Vosseler definió la eficiencia de la línea de producción como la relación entre cuánto tiempo la máquina produce piezas buenas a máxima velocidad, comparadas con el tiempo que la máquina disminuye su velocidad o se detiene debido a problemas técnicos, alarmas o mantenimiento.
En base a las mejores cifras de producción y calidad para las líneas de producción reconstruidas, Univent le pidió a Autefa construir e instalar otras 20 máquinas adicionales de producción de mascarillas para el 2021. Luego de la instalación y puesta en marcha de estas nuevas máquinas, Univent calcula que va a producir de 3.5 a 4 millones de respiradores Atemious Pro FFP2 a la semana, y convirtiendo a la compañía en uno de los más grandes productores de respiradores FFP2 en Europa.
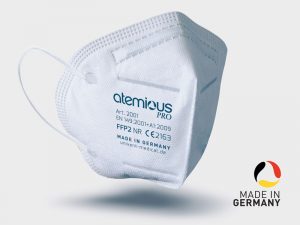
El Respirador Atemious Pro FFP2
El respirador de filtrado modelo Atemious Pro es construido para superar los estándares de ensayos del Conformité Européenne(CE) FFP2, y ha sido demostrado en ensayos que puede capturar más del 98% de las partículas pequeñas sólidas y líquidas que expanden el Covid-19. Al igual que el respirador N95, con el cual se puede comparar su rendimiento y desempeño (el N95 es el respirador estándar aprobado por el U.S. National Institute for Occupational Safety and Health (NIOSH), el respirador Atemious Pro, de Univent, forma un sello a prueba de aire con la cara del usuario, de modo que su diseño no solo debe balancear una excelente filtración de las partículas con el confort del usuario, sino que también debe minimizar cualquier resistencia de exhalación añadida que puede causar fatiga al usuario durante horas de uso.
Aunque muchas mascarillas quirúrgicas y respiradores de filtración utilizan una lámina de tres capas de tejido no tejido, el respirador Atemious Pro utiliza cuatro capas, las cuales son bondeadas o unidas usando soldadura ultrasónica. La más próxima a la piel es una capa hecha de fleece que absorbe la humedad. Luego, en el interior, hay dos capas especiales que realizan la filtración de partículas finas, y que son construidas de una napa muy apretada de fibras de polietileno usando el tipo de no tejidos meltblown.
Esto es terminado en la parte externa por una cobertura exterior protectora de fleece de polietileno y el cual provee la resistencia estructural. Para asegurar un ajuste apretado pero confortable a la vez, los tejidos laminados en el respirador incorporan un puente ajustable para la nariz, y puntos de adhesión superior/inferior para una banda para las orejas suave y estirable, y que también están disponibles con anillos o bandas para la cabeza.
Nota del Editor: Didier Perret es Gerente de Desarrollo de Negocios Médicos, Branson Soldadura y Ensamblajo, en Emerson
Marzo-Abril de 2021