E
n la industria textil de la actualidad, los ahorros de energía no son solo deseables sino
que son esenciales. Los argumentos para ésto se han vuelto aún más críticos, debido al crecimiento
de los costos y a las presiones competitivas, a las limitadas reservas de petróleo y gas, y a los
mayores embotellamientos energéticos relacionados con una mayor demanda por productos textiles
causados por el crecimiento económico y de la población, particulamente en los mercados emergentes.
En China y la India, por ejemplo, los precios actuales por kilovatio hora (kWh) de
electricidad son los más altos en el mundo, y por lo tanto, estos precios ejercen una gran
influencia en estos importantes países fabricantes de hilados industriales.
Por consiguiente, los requerimientos enérgeticos para la manufactura de hilados se
convierten en un factor de costo importante: un sistema convencional de IDY/poco encogimiento, por
ejemplo, consume alrededor de 6.4 millones de kWh de electricidad al año para la producción de
10.000 toneladas. En la India, este costo es de alrededor de $640.000 dólares.
“En vista de tales cantidades, los clientes se están enfocando en la actualidad – además de
la calidad – en la producción de tejidos industriales para llantas, carpas de lona, bandas
transportadoras, geotexiles, e hilados de costura, que sean eficientes en energía”, declaró Arnulf
Sauer, Jefe de Electrónica & Software, de Oerlikon Barmag.
Este desarrollo confirma la ruta en la que se ha embarcado la división de Oerlikon Textile y
sus empresas asociadas desde mediados de la década de los 1990, con énfasis especial en el programa
de ahorro eficiente de energía, “e-save”, y la producción eficiente de procesos “energy-aware”.
Correspondientemente, máquinas y procesos certificados se destacan en términos de procesos amenos a
los recursos, y consumen menos energía que los estándares del mercado, con ahorros totales de hasta
un 25% o más.
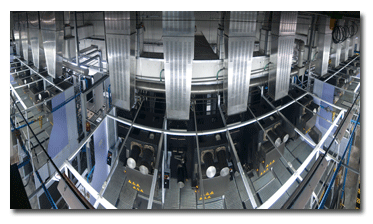
Una moderna planta de hilado industrial instalada recientemente en Brasil, y la cual fue
creada de acuerdo a las reglas tipo “e-save” (e-ahorro).
Ahorros de energía
En una máquina tipo IDY, el consumo principal de energía se relaciona generalmente con los
siguientes procesos: mando del extrusor (21% del consumo general); sección de hilatura (15%); mando
de recogida o enrollado (25%), y calentamiento de la rueda estiradora (35%).
El mando de la extrusora ofrece considerables ahorros potenciales, ya que alrededor del 97%
de los costos de operación en la duración útil de este mando se relaciona exclusivamente con su
consumo de energía. “Hemos reducido este consumo utilizando motores hechos de materiales superiores
y con una mayor relación de cobre y por lo tanto una mayor conductividad así como una optimizada
tecnología de ventilación”, explicó Sauer.
Mandos correspondientes con la más alta clase de eficiencia en Europa, EFF-1, consumen
alrededor de un 2% menos energía que los motores estándares. Esto puede parecer como un ahorro
mínimo. Sin embargo, una extrusora tipo Oerlikon Barmag 17E10/24D (de 175 mm de diámetro), puede
ahorrar 3.6 kWh por hora de esta manera. Cuando se calcula todo un año de funcionamiento,
totalizando 8.400 horas, esto representa un ahorro de más de 30.000 kWh – ó sea de alrederedor de
$3.800 dólares (si el costo es de $0.10 por kWh). Por lo tanto, la extrusora alcanza el punto de
recuperación de la inversión en menos de un año.
En comparación con un sistema de la competencia, el consumo de energía del plegador de
hilatura SP8X, se redujo en un 45%. La cabeza de hilatura es calentada a alrededor de 300 °C para
asegurar que el derretido de hilatura permanezca en un estado de flujo libre y se pueda presionar a
través de la tobera de hilatura usando bombas de hilatura. El secreto para esto es en la
construcción redonda de la sección transversal en lugar de la construcción rectangular que es el
estándar en el mercado, ya que esto reduce la superficie que debe ser calentada y por lo tanto
reduce el consumo de energía.
Por consiguiente, los ahorros potenciales de energía para la sección de hilatura totalizan
alrededor de $22.800 dólares en la producción de IDY, asumiendo un volumen de producción de 10.000
toneladas al año y un costo de $0.10 dólar por kWh.
El Sistema de Calentamiento Godet (tobera de hilatura), patentado por Oerlikon Barmag,
también funciona de manera más eficiente que el estándar del mercado. La tecnología de alta
frecuencia (HF) es usada para calentar las toberas de hilatura por encima de la cual el hilo es
halado o estirado. En contraste con los sistemas convencionales de 50 herzios, este sistema utiliza
tecnología de inducción, con hasta 10 kHz y solo genera calor cuando se requiere realmente, o sea
en la superficie exterior del casco de la tobera de hilatura.
De acuerdo a esto, las toberas de hilatura de múltiples zonas HF consumen alrededor de un
25% menos de energía. Dependiendo del producto que se está manufacturando, esto puede proveer
ahorros, desde $6.300 dólares hasta $7.100 dólares al año por posición.
Para sumarizar, los ahorros totales para un sistema IDY generan cálculos interesantes para
la producción de 10.000 toneladas de hilado al año: se utilizan dos extrusoras para proveer ahorros
colectivos de $7.600 dólares. Los sistemas de hilatura y de Godet (tobera de hilatura), ahorran
respectivamente entre $22.800 y $50.000 dólares – ofreciendo así ahorros anuales potenciales de más
de $80.000 dólares para un solo sistema.
“Y esto no tiene en cuenta el hecho que las máquinas IDY ofrecen más ahorros potenciales ya
que proven una mayor producción por unidad que los sistemas suministrados por la competencia”,
agregó Sauer. En general, los sistemas de producción de hilados industriales de Oerlikon Barmag,
consumen un 25% menos de energía que los estándares del mercado.
Julio-Agosto de 2009