Las nanofibras (fibras muy pequeñas) han mostrado durante mucho tiempo una gran promesa para el
mejoramiento del desempeño en los textiles y materiales en aplicaciones que van desde la filtración
de aire y de líquidos hasta separadores de baterías, y desde el aislamiento de los ruidos y
barreras para fluidos en productos de uso higiénico. Así por ejemplo, en la filtración, se ha
mostrado, de manera teórica y empírica, que las nanofibras proveen escalas de caída de la presión
excepcionales a través de la acción del efecto de flujo deslizante que no se puede lograr con
fibras voluminosas. También son apropiadas para permitir el mecanismo de filtración de la Difusión
Brownian, que puede capturar materias de partículas de 0.5 micrones y más pequeñas.
Las nanofibras también imitan la matriz extracelular que permite la propagación de las
células vivas en el cuidado de las heridas y en la formación de tejido humano.
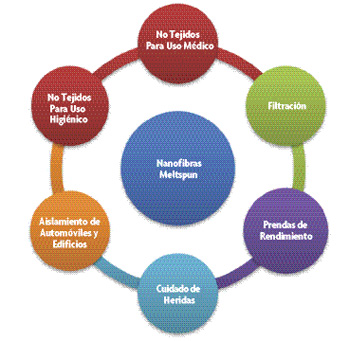
En dirección de las manecillas del reloj, comenzando con la fotografía de la parte
superior: Los mercados actuales y futuros para las nanofibras tipo melt-spun incluyen a no tejidos
para uso médico, filtración, prendas de alto desempeño, cuidado de heridas, y no tejidos para
aislamiento y para usos higiénicos.
Estas fibras, que generalmente se describen en términos comerciales como fibras con un
diámetro menor a 1 micrón, han sido el sujeto de intensos estudios durante algún tiempo.
Ciertamente, en la literatura se revela un extenso campo de investigación y el reporte de
mejoramientos en el desempeño de estas fibras.
Es difícil encontrar una universidad que no posea una aguja de electro-hilatura, aún si es
rudimentaria, que se esté usando para demostrar los avances en el rendimiento de los materiales que
ocurren en la escala nano de cosas pequeñísimas. Las instituciones académicas han aplicado una gran
diligencia en la caracterización y el reporte de estos desarrollos.
Además, una búsqueda de patentes revela rápidamente que muchas de las mayores compañías
mundiales fabricantes de textiles, no tejidos, y tejidos para filtración, no solo han realizado
intensos esfuerzos de investigación y desarrollo en esta área, sino que también han realizado
inversiones significantes para proteger sus posiciones.
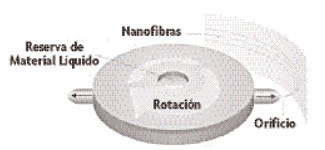
Las tecnologías de nanofibras por fusión incluyen la tecnología de meltblown (abajo), por
cortesía de Atul Dahiya, “Meltblown Technology”; y tecnología Forcespinning® (arriba), por cortesía
de FibeRio Technology Corp.
Comercialización
Sin embargo, es claro que todavía no se ha realizado el potencial total de la
comercialización de la tecnología de nanofibras. En el año 2010, BCC Research LLC, de Wellesley,
Mass., calculó que el entero mercado para productos de nanofibra llegaría a aproximadamente $183
millones de dólares para el 2012.
En comparación, la producción de microfibras en la actualidad es de varios miles de millones
de dólares al año y está creciendo rápidamente, de acuerdo a International Nonwovens Consulting, de
Raleigh, N.C.
Sin embargo, Donaldson Filtration Co. Inc., de Bloomington, Minn., fue el pionero de los
filtros de nanofibra a mediados y finales de la década de los 1980s. Esto no fue mucho después de
que las microfibras de tipo meltblown o derretidas por fusión comenzaron a tener aplicaciones en el
mercado, y cuando comenzaron a proliferar las líneas Reicofil de spunbond-meltblown-spunbond (SMS).
Al evaluar el activador detrás de esta divergencia, hay que mirar a las diferencias entre
los procesos basados en fusión o derretido y los procesos que hacen un uso intenso de los
solventes, tales como la electro-hilatura (electrospinning). Ciertamente, el principal desafío en
la electro-hilatura de escala ha sido las altas concentraciones de solvente a polímero necesarias
para producir la nanofibra.
El uso mayor de solventes conduce a una producción menor, incrementa dramáticamente los
costos de operación, así como la carga ambiental, lo que es contrario a los vastos esfuerzos de
sustentabilidad que se están llevando a cabo en la actualidad en la mayoría de las compañías
textiles y para no tejidos.
En una reciente conferencia realizada en Japón, varias compañías líderes en el campo de la
electro-hilatura reportaron sobre el trabajo realizado en esta área, pero los datos demostraron
claramente que existen desafíos significantes para la conversión de la electro-hilatura a un
proceso basado en fusión.
En un esfuerzo realizado para finalmente comenzar a transferir el pleno potencial de la
tecnología de nanofibras a productos finales, las principales compañías productoras de materiales
se han encarado a los desafíos de la productividad y la responsabilidad con el medio ambiente,
adquiriendo procesos basados en fusión como plataformas que serán usadas ventajosamente en el
futuro.
Estos esfuerzos han iniciado una nueva era que va más allá de la electro-hilatura y que se
enfoca en la tecnología de producción de nanofibras por fusión. En este artículo se presentan dos
plataformas de procesos que existen en la actualidad, y cuyos materiales están disponibles en forma
de fibras; los mercados a corto plazo para las aplicaciones finales; y las posibilidades ilimitadas
que son creadas cuando hay una disponibilidad de nanofibras casi sin límites.
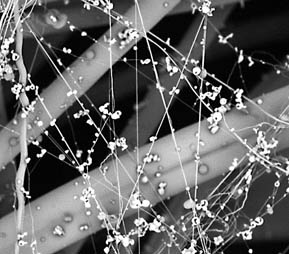
El uso de procesos de producción basados en fusión expandirá el uso de las nanofibras en
aplicaciones de filtración del aire.
Procesos de nanofibra por fusión
El meltblown (soplado por fusión) es un proceso de una etapa en el que aire calentado a alta
velocidad sopla sobre una resina termoplástica derretida, desde la punta del molde de un extrusor
en un conveyor o pantalla de enrollado para crear fibras. Desarrollado originalmente en su forma
comercial por la firma Exxon a finales de la década de los 1970s, el meltblown ha probado ser muy
útil para la elaboración de fibras con diámetros en el rango de decenas de micrones y más altos,
pero el enfoque de la mayor parte del desarrollo de esta tecnología ha sido hacia mayores
velocidades de la línea y hacia la integración en líneas de spunbond.
Recientemente, los esfuerzos se han alejado de la producción de altos volúmenes y se han
dirigido hacia fibras más finas para alcanzar un mejor desempeño en la filtración de aire.
Investigaciones realizadas en Alemania y los Estados Unidos se han enfocado casi exclusivamente en
el polipropileno (PP) y han mostrado ganancias en la generación de fibras en el rango de
sub-micrones.
Los desafíos encarados para reducir aún más el diámetro de la fibra incluyen la importancia
de incrementar la relación del flujo de masa de aire a polímero. Esta mayor relación lleva a la
necesidad de producir velocidades de aire muy altas y tasas de alimentación de polímero limitadas,
lo que aumenta los costos de operación y limitan la productividad. Otro desafío es la amplia
distribución de los diámetros de la fibra, que pueden ejercer un impacto significante en el
desempeño de la filtración de aire.
Recientemente, se ha expandido el trabajo más allá del PP, y un grupo de la Universidad de
Tennessee ha obtenido avances en el procesamiento de nanofibras hechas de ácido poliláctico (PLA).
El PLA es deseado como un termoplástico amigable al medio ambiente, y con beneficios en el
desempeño del material. A medida que se continúa expandiendo el trabajo de investigación del
meltblown en nuevos materiales, se incrementarán también las aplicaciones del mismo.
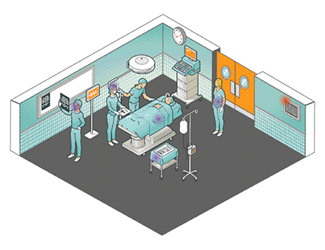
Las aplicaciones de las nanofibras para no tejidos médicos incluyen batas quirúrgicas
desechables, cortinas y coberturas para bandejas.
Tecnología Forcespinning®
La tecnología de Forcespinning® (hilatura forzada) utiliza fuerza centrífuga para procesar
materiales y convertirlos en nanofibras. Una copa de tobera de hilatura es girada a altas
velocidades para iniciar la acción de fuerzas hidrostáticas y de corte, que empujan un material
líquido, ya sea derretido o en solución, a través de orificios colocados en la pared exterior de
una tobera de hilatura. A medida que el material entra a la cámara del orificio, las moléculas se
separan y luego se alinean en una misma dirección para formar nanofibras.
Esta tecnología exclusiva ha sido desarrollada recientemente para producción a nivel
comercial, por la firma FibeRio Technology Corp. de McAllen, Texas, y ya ha logrado un impulso
significante con el reporte de la producción de nanofibras de PP con diámetros promedios de menos
de 500 nanometros (nm).
Además, una producción con un incremento de 100 veces mayor en las tasas de productividad ha
permitido que esta tecnología se pueda consi-derar para algo más que en aplicaciones para el
filtrado de aire. Se han demostrado ganancias dramáticas en la productividad, tanto con los
procesos basados en fusión como en los procesos de hilatura por solución gracias a niveles de
concentración de polímeros mucho más altos que en el caso de la electro-hilatura.
Otros materiales que se han hilado por el método de fusión (melt-spun) incluyen el PLA, el
tereftalato de polibutileno (PBT), el tereftalato de polietileno (PET), las poliamidas (PA), el
fluoruro de polivinilodino, el polietileno de bajo peso molecular, y el poliuretano termoplástico.
Las aplicaciones son, por lo tanto, increíblemente variadas, y van desde prendas de vestir de gran
desempeño hasta la filtración de fluidos y más.
Sin embargo, el potencial pleno de la tecnología Forcespinning surgirá cuando FibeRio fije
su vista en el procesamiento de plásticos ingenierizados por el procesamiento de fusión para
convertirlos en nanofibras.
Aplicaciones de nanofibras melt-spun
Las siguientes son las principales aplicaciones de las nanofibras desarrolladas por el
proceso de hilatura por fusión (melt-spun):
No tejidos para uso médico: La firma Global Industry Analysts Inc., de San José, California,
calcula que el mercado global para no tejidos de uso médico desechables alcanzará $20.900 millones
de dólares para el año 2017. Aplicaciones en esta área incluyen batas quirúrgicas, cortinas y
coberturas de bandejas. Las nanofibras de PP tipo melt-spun se pueden utilizar para proveer
desempeños de barrera respirable requeridos en dichos productos.
Durante el pasado año, FibeRio reportó mejoramientos significantes en el desempeño
relacionado con la barrera de agua, con casi 60 milibar de cabeza hidrostática — un valor que
satisface el Nivel 3 del estándar PB70 de la Asociación para el Avance de Instrumentos Médicos
(AAMI por sus siglas en inglés) — con solo 6 gramos por metro cuadrado (gm2) de material, comparado
con el tradicional 15 gm2 de material para microfibras de tipo meltblown, haciendo que el tejido
sea de poco peso y respirable gracias al uso de medios equipados con nanofibras.
Filtración: Las nanofibras se han usado durante algún tiempo en aplicaciones para el
filtrado de aire. Sin embargo, el uso de procesos basados en fusión expandirá su uso en dicho
mercado. Las nanofibras de PP tipo melt-spun, obtenidas con tecnologías ya sea meltblown o de tipo
Forcespinning, han demostrado calificaciones de alta eficiencia con caídas de presión baja. Las
calificaciones de eficiencia son accionadas por la utilización de la Difusión Brownian, mientras
que el desempeño en la caída de la presión se puede atribuir al flujo de deslizamiento en la
superficie de la fibra.
Estos beneficios crean una oportunidad significante para muchas compañías en el campo de la
filtración, debido a que las instituciones de regulación se han dedicado recientemente a eliminar
la práctica histórica del cargado electrostático de los medios para alcanzar calificaciones de alta
eficiencia, como es demostrado por la norma europea EN779:2012.
Sin embargo, a medida que continúa disminuyendo el diámetro de la fibra, se están haciendo
disponibles nuevas aplicaciones, tales como el filtrado de agua. Se están creando oportunidades
significantes con el uso de nanofibras de PP tipo melt-spun y PET, para alcanzar tamaños de poro
comparables a aquellos de membranas, al mismo tiempo que se provee una caída de presión más baja de
los medios fibrosos. Además, las nanofibras de PBT su pueden usar en aplicaciones de filtración de
combustibles y de separación de la sangre.
Prendas de Alto Desempeño: recientemente, las nanofibras han encontrado su camino al campo
de productos finales tales como calcetines, chaquetas, e incluso guantes para golf. Los materiales
usados han variado, desde PA 6 a PET. Se cree que estos procesos fueron del tipo basado en
solventes y es razonable esperar que la emergencia de nanofibras de PET tipo melt-spun, con sus
mayores capacidades de producción anual y sus menores gastos de operación, podrían incrementar
substancialmente el uso de las nanofibras en estas aplicaciones.
Cuidado de Heridas: El manejo de la humedad es accionado por el control sobre la porosidad,
y esta es la razón por la que las nanofibras han surgido como una herramienta crítica en la
industria del cuidado de las heridas. Además, los materiales deben ser al menos compatibles
biológicamente y, preferiblemente en algunos casos, bio-reabsorbibles, o sea con la capacidad de
ser absorbidos de nuevo.
En estos casos, el residuo tóxico dejado por los solventes son un impedimento y limitan las
oportunidades comerciales. Las nanofibras de PLA tipo melt-spun y, en el futuro, las fibras de
policaprolactano tipo melt-spun, superarán este desafío al mismo tiempo que aumentarán la
productividad.
Aislamiento acústico: La conciencia sobre la protección del medio ambiente y los costos
crecientes de los combustibles han llevado el término de “peso liviano” a la parte frontal del
léxico de la industria de transporte automotriz y aeroespacial. A este respecto, las nanofibras
permiten que los abastecedores de productos para automóviles puedan reducir substancialmente el
peso de los materiales al mismo tiempo que mejoran el desempeño del aislamiento acústico.
El desafío hasta ahora ha sido la sensibilidad a los costos y los altos volúmenes de tal
industria. Sin embargo, las nanofibras tipo melt-spun superan este desafío, y las fibras de PP y
PET son resinas que ya son familiares en esta industria.
Direcciones para el futuro
A medida que se amplía la gama de materiales utilizados, otra área que está siendo evaluada
es el uso de las nanofibras en las dispersiones y como reforzamientos en compuestos. Las fibras de
escala tipo nano o minúsculas tienen la capacidad de una distribución uniforme en una matriz de
polímero y tienen una gran promesa para mejorar la resistencia a la rotura, así como para
regularizar la viscosidad, y para mejorar otras propiedades.
Las nanofibras de fibra cortada están comenzando a ser consideradas por los ingenieros de
materiales y podrían tener vastas aplicaciones más allá de los reforzamientos de compuestos. La
manufactura de volúmenes, de costo efectivo, permitirá que estas aplicaciones sean posibles
comercialmente.
Otros mercados que subirán a bordo a medida que el procesamiento de las nanofibras alcanza
una alta productividad y un escalamiento de la velocidad de la línea será en aplicaciones en no
tejidos usados en la higiene. A medida que los abastecedores de etiquetas privadas continúan
aumentando su participación en el mercado, los abastecedores de productos de marca están buscando
por nuevos caminos de diferenciación. Este desarrollo ha llevado a una búsqueda por tecnologías que
proveen materiales más delgados y que aumentan la capacidad de manejo de los fluidos.
Los esfuerzos en las tecnologías de tipo meltblown y Forcespinning están removiendo los
costos asociados con la productividad, los gastos de operación, y las barreras impuestas por la
protección al medio ambiente. A medida que se superan los obstáculos finales para la producción de
nanofibras en alto volumen, la conversación se alejará de los desafíos relacionados con los
procesos y cambiará hacia el desarrollo de nuevos productos finales y la propiedad intelectual
requerida para competir.
El futuro de las nanofibras está preparado para cualquier tipo de aplicaciones que buscan la
forma de reducir el peso al mismo tiempo que mejoran el desempeño del material. El procesamiento
por fusión permite también el uso de nuevos materiales que son más amenos para la protección del
medio ambiente y que se pueden usar para aplicaciones existentes.
Además, se posibilita el uso de nuevas capacidades a través de la utilización de nuevos
materiales tales como materias aromáticas, sulfonas, fluoropolímeros, y uretanos. Estos materiales
ya han demostrado una gran promesa al nivel de investigación, y los nuevos desarrollos lo escalarán
rápidamente a la producción industrial continua.
Bryce W. Davis, Ph.D., es Ingeniero de Materiales; y Kial Gramley es vicepresidente de
marketing y desarrollo de negocios, de FibeRio Technology Corp. Se incluye una bibliografía en la
versión Online de este artículo en el sitio
Textilespanamericanos.com
Mayo-Junio de 2013